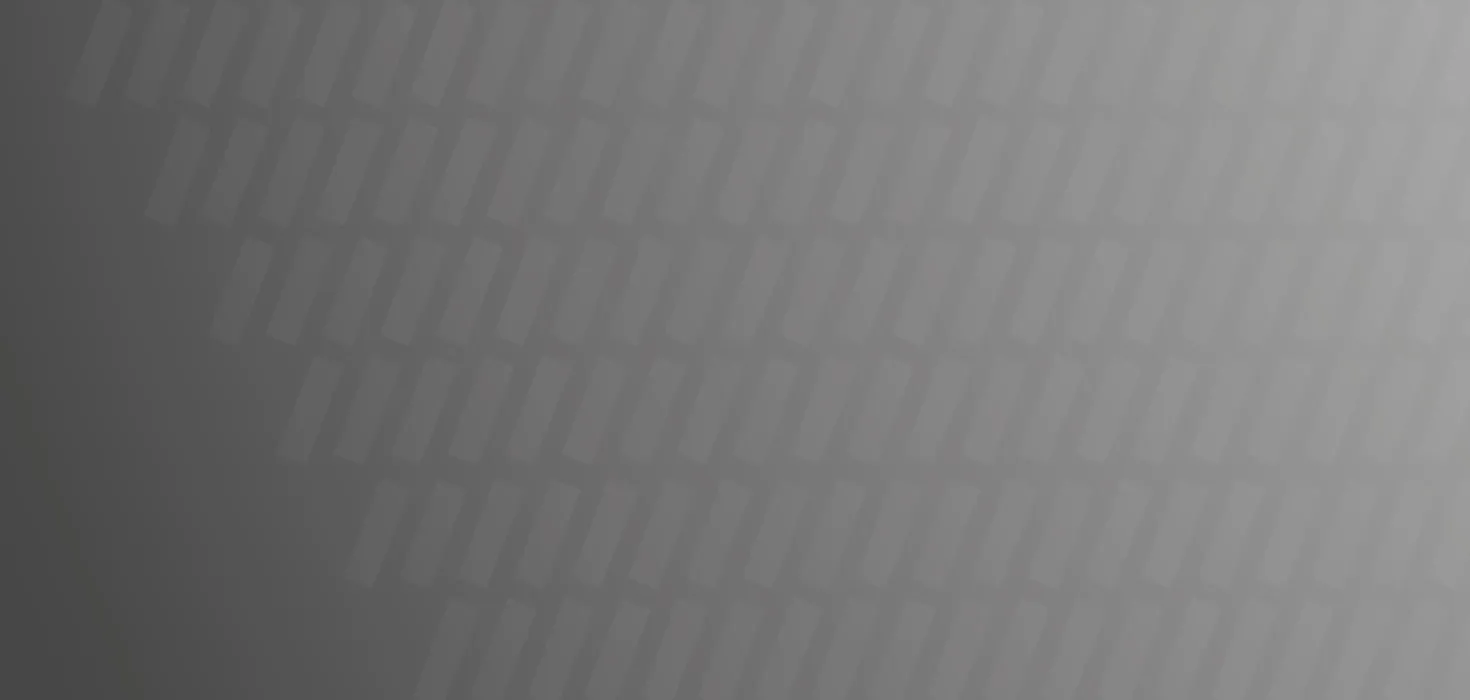
Abwasserreduzierung in der Papierindustrie mit Membranbioreaktor
Abwassereinsparung
Frischwassereinsparung
Prozessdampfeinsparung
CO2-Reduktion
Faserstoffrückgewinnung
Köhler Pappen verarbeiten zum Großteil Altpapier in unterschiedlichsten Sorten. Für die Verarbeitung ist eine große Menge an Wasser von Nöten, die bisher zu 100 % an die kommunale Kläranlage weitergegeben wurde. Um Kosten und Ressourcen zu sparen hat das Unternehmen sich zum Ziel gesetzt, das eingesetzte Wasser zu großen Teilen in einem Wasserkreislauf in die Produktion zurückzuführen.
Für Köhler Pappen sind Umweltschutz und Nachhaltigkeit keine Schlagworte, sondern integraler Bestandteil der Geschäftstätigkeit. So verarbeitet das Unternehmen 95 % Altpapier. Durch die hohe Sortenvarianz, insbesondere durch stark gefärbte Pappen, werden hohe Anforderungen an den Wasserkreislauf und die Wasseraufbereitung gestellt.
Für die Herstellung der Pappen werden ca. 300 m³ Wasser pro Stunde benötigt. Das anfallende Produktionsabwasser wurde bisher nach einer mechanischen Vorreinigung zu 100 % an die kommunale Kläranlage abgegeben.
Aufgrund steigender Abwasserkosten sollte das Wasser zukünftig so aufbereitet werden, dass es großteils in die Produktion zurückgeführt werden kann. Hierfür musste ein geeignetes Verfahren gefunden werden, welches das Produktionswasser in mehreren Schritten bis zur entsprechenden Qualität aufbereitet. Dazu wurde die Verwendung eines Membranbioreaktors in Betracht gezogen.
Die deutliche Reduzierung der Abwassermenge, respektive des Frischwasserbedarfs, stellt einen wichtigen Beitrag zur Ressourcenschonung dar. Die Konsequenzen des geplanten Verfahrens sollten in einer separaten Umweltbetrachtung (Wirkungsanalyse) abgeschätzt und dokumentiert werden.
Es sollte eine Abwasserbehandlungsanlage mit einer Abwasserwiederverwendung nahe 100 % ohne qualitative Einbußen bei der Produktqualität gebaut werden. Das mechanisch vorgereinigte Abwasser sollte in weiteren Stufen in einem Membranbioreaktor (MBR) gereinigt werden. Der Membranbioreaktor ist eine Kombination zwischen konventionellem Belebungsverfahren und Membranfiltration (Ultrafiltration).
Die zusätzliche Verwendung einer Umkehrosmose (Nanofiltration) dient zur Entsalzung des Filtrats und sollte zu einem Optimum an Wasserqualität führen. Durch diese technologische Ergänzung sollte eine Rückführquote des Wassers von über 90 % erreicht werden.
Das Konzept setzte auf der vorhandenen Vorklärung, einer Sedimentation, auf. Ein unumgänglicher Prozessschritt war im weiteren Verlauf der Abwasserreinigung eine Enthärtung durch den High-Rate-Clarifier (HRC). Dies wurde notwendig, da der hohe Kalziumeintrag über das Altpapier das Prozesswasser sehr hart macht.
Die Wasserhärte führt bei Änderung der Prozessparameter, z. B. pH-Wert, Temperatur, Leitfähigkeit, zu Ablagerungen in der Belebung, an den Membranen des Membranbioreaktors sowie in der Pappenproduktion. Dies kann die Prozesse massiv behindern. Daher wird ein Teil des gelösten Kalziums durch Zugabe von Kalziumhydroxid und Soda gezielt im HRC ausgefällt und das Abwasser teilenthärtet.
Anschließend wird das Abwasser mit einem Plattenwärmetauscher gekühlt und gelangt in die biologische Klärstufe. Die aerob betriebene biologische Klärstufe besteht aus drei Kaskaden und wird mit einer Belebtschlammkonzentration von 8-10 g/l betrieben. Als wesentlicher verfahrenstechnischer Baustein fungiert hier das Membrane Operating System (MOS), das die Funktion der Schlammtrennung erfüllt. Es umfasst eine Membranfläche von 5.400 m² verbaut in drei Becken á 15 m³.
Das Belebtschlamm-Luft-Gemisch wird hier mit Hilfe des patentierten Mem-Jet-Verfahrens eingedüst. Die daraus resultierende optimierte Anströmung der Membrane führt zu einer intensiven Reinigung der Membranoberflächen im laufenden Betrieb, welche höhere spezifische Durchsatzraten und längere Reinigungsintervalle bewirkt. Das MOS-System besteht aus drei parallelen Strängen. Dies ermöglicht eine vollautomatische Reinigung der Membranen während des laufenden Betriebes ohne Änderung an der Hydraulik.
Nach der MBR-Anlage ist eine Teilstrombehandlung mit Umkehrosmose installiert. Mit dieser wird die Leitfähigkeit für das Prozesswasser der Produktion gesenkt und Ablagerungen vermieden. Dadurch wird es möglich, 90 % des ultrafiltrierten Abwassers ohne Qualitätsverluste im Produkt wieder in der Produktion zu verwenden.
Der anfallende Kalkschlamm und Belebtschlammüberschuss werden als Füllstoff für die Pappe in den Produktionskreislauf zurückgeführt. Dadurch werden die für den Schlamm anfallenden Entsorgungskosten eingespart.

Die neue Abwasserbehandlungsanlage reduziert die Abwassermenge um ca. 90 %. Das entspricht über 250.000 m³/Jahr. Der Bedarf an Frischwasser konnte um mehr als 70 % gesenkt werden, was einer Wassereinsparung von über 200.000 m³/Jahr entspricht.
Durch die Rückführung des warmen Prozesswassers konnte der Bedarf an Prozessdampf um 3.500 MWh/Jahr gesenkt werden und damit auch die Energiekosten. Dementsprechend wurde der jährliche CO2-Ausstoß um 750 t verringert.
Überdies gehen die im Abwasser enthaltenen Fasern nun nicht mehr durch die Einleitung in die kommunale Kläranlage verloren, sondern werden zurückgewonnen. Hierbei wird eine Faserstoffrückgewinnung von ca. 25 t/Jahr erzielt.
Um ein innovatives Forschungs- und Entwicklungsprojekt wie die Membrantechnik in der Papierindustrie realisieren zu können, war im Vorfeld des Vorhabens eine Pilotierung notwendig. Mit Siemens konnte ein leistungsstarker Partner gewonnen werden, der eine Pilotanlage im Maßstab 1:50 herstellte. Diese Anlage wurde für mehr als drei Monate in einen Teilstrom des Abwassers intergiert, um das Verhalten der Membrane bei spezifischem Abwasser aus der Altpapieraufbereitung zu erforschen. Viele Werte, wie z. B. Scaling, Fouling und Veränderungen der Druckverhältnisse, konnten so ausgewertet werden. Diese Daten waren wichtige Bausteine und Entscheidungshilfen für den Anlagenbau und die Auslegungsparameter des endgültigen F&E-Projekts.
Die Erfahrungswerte nach rund einem Jahr im Vollbetrieb hatten gezeigt, dass die Behandlung des gesamten Abwassers weitere Erkenntnisse brachte. Die Ergänzung einer Enthärtungsanlage (Entkalkung) wurde notwendig. Die chemischen Reinigungen wurden nicht mehr nach den Herstellervorgaben, sondern mit den Erfahrungswerten aus dem Realbetrieb durchgeführt. Eine Anpassung, die sich sehr positiv auf die Lebensdauer der Anlage auswirken sollte. Unzählige Wasserparameter wurden kontinuierlich erfasst, wodurch die Anlagenleistung signifikant gesteigert werden konnte.
Nach sieben Jahren Erfahrungen, lässt sich heute sagen, dass ein stabiler und wirtschaftlicher Anlagenbetrieb trotz aller Einflüsse und Schwankungen aus dem Altpapier möglich ist und täglich realisiert wird. Es ist daher erstaunlich, dass das umgesetzte Anlagenkonzept in der Branche nach wie vor einzigartig ist.
In Gengenbach, im schönen Schwarzwald, pflegt Köhler Pappen eine langjährige Tradition des verantwortungsbewussten Umgangs mit Natur und Umwelt. Deshalb setzt Köhler Pappen bei seiner Produktion auf Recycling.
Die Pappenfabrik Albert Köhler GmbH & Co. KG ist einer der führenden Hersteller für Grau- und Wickelpappen. Das Unternehmen besteht am Standort Gengenbach seit dem Jahr 1873. Mit 100 Mitarbeiterinnen und Mitarbeitern werden auf zwei Wickelpappenmaschinen und einer Langsiebmaschine verschiedene Pappenqualitäten hergestellt. Die durchschnittliche Produktionsmenge der letzten Jahre lag bei ca. 40.000 t für Ordner, Bücher und Puzzlespiele, Pappen für die Möbelindustrie sowie Werbungs- und Displayprodukte. Die Marktgebiete sind zu 35 % in Deutschland und 65 % im Export.
Zertifizierungen, wie Energiemanagement DIN ISO EN 50001, PEFC und FSC, dienen zur Umsetzung der hohen Qualitätsanforderungen der Produkte.

- Großserienfertigung ,
- Prozessindustrie
- Unterstützungsprozesse / Gebäudemanagement
- GreenTech BW ,
- Dämmung / Isolation ,
- Prozessoptimierung ,
- Stoffkreislauf / Recycling
- Energie ,
- Material ,
- Trinkwasser ,
- Abwasser ,
- Abgas
- strategisch (größer 5 Jahre)