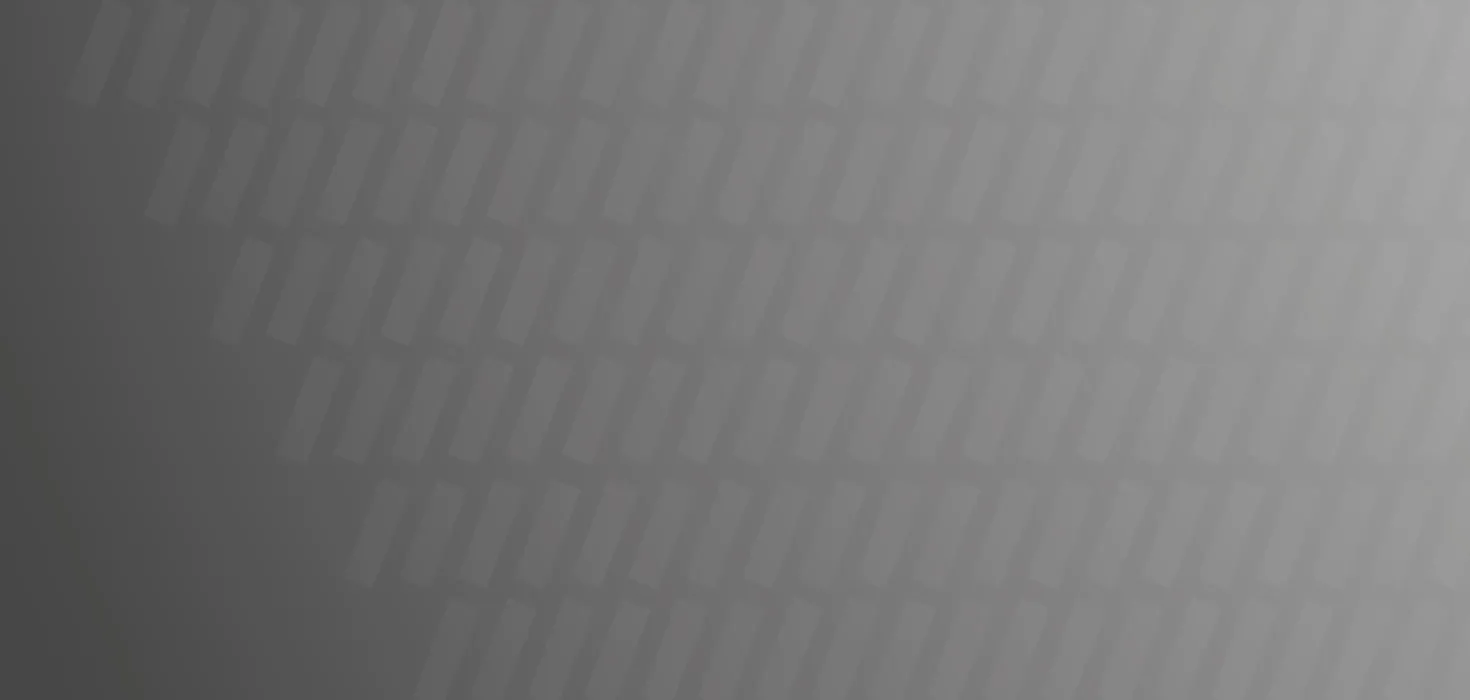
Energetische Sanierung der technischen Gebäudeausrüstung
Energieeinsparung (elektisch)
CO2-Reduktion
Die Mayer & Cie. GmbH & Co. KG ist der weltweit führende Hersteller von Rundstrickmaschinen. Das Unternehmen hat ein altes Betriebsgebäude saniert und energetisch optimiert, um Energie einzusparen. So können zukünftig nicht nur Nebenkosten eingespart werden. Auch für die Entwicklungen des Energiemarkts und für neue Arten der Energieversorgung ist das Unternehmen zukünftig gewappnet.
Kostenvorteile
ca. 650.000 Euro/Jahr durch Energieeinsparungen
Die Mayer & Cie. GmbH & Co. KG ist der weltweit führende Hersteller von Rundstrickmaschinen. Das Portfolio umfasst 50 Rundstrickmaschinentypen, auf denen Stoffe für die Automobilindustrie, Heimtextilien, Sport-, Nacht- oder Badebekleidung hergestellt werden können. Von der Entwicklung bis zum Verpacken der Maschine deckt der Standort Albstadt alle Prozesse eines modernen Maschinenbauunternehmens ab.
Die Gebäudetechnik am Standort ist seit den Anfängen des Unternehmens im Jahr 1905 baulich gewachsen und war nicht mehr energieeffizient und oft überdimensioniert. Die Nebenkosten und der Energieeinsatz des Unternehmens waren demnach nicht verhältnismäßig für die wettbewerbsintensive Textilindustrie.
Mit der Festsetzung des Energiemanagements in der Unternehmensstrategie 2013 wurde der Grundstein zu einem nachhaltigen Umgang mit Ressourcen gelegt. Mit der darauffolgenden Einführung des Energiemanagementsystems nach DIN EN ISO 50001 wurde mit der IST-Aufnahme des Energiebedarfs und der Energieverbraucher begonnen. Ziel war es, den Energieverbrauch stetig zu senken und die Effizienz der technischen Gebäudeausrüstung zu erhöhen.
Zuerst sollte der tatsächliche Energiebedarf erfasst, die Verbraucher nach Höhe der Verluste gegliedert und die notwendigen Maßnahmen zur Steigerung der Energieeffizienz katalogisiert werden. Die Umsetzung der Maßnahmen sollte in zwei Phasen erfolgen. In der ersten Phase sollten zunächst die in der IST-Analyse festgestellten Maßnahmen umgesetzt werden. Anschließend sollten in der zweiten Phase durch die Realisierung eines Kraft-Wärme-Kälte-Konzepts (KWKK) die Grundlasten der Wärme-, Kälte- und elektrischen Leistung des Unternehmens abgedeckt werden.
Die strukturierte Umsetzung des Maßnahmenpakets der ersten Phase begann im Jahr 2014 mit der Sanierung des Kaltwassernetzes, da hier das größte Einsparpotenzial erkannt wurde. Durch die disziplinierte Messung des tatsächlichen Kältebedarfs konnten drei von neun Kältemaschinen außer Betrieb genommen werden. Dazu war es erforderlich, dass eine Verbindung zweier bisher getrennter Netze hergestellt wurde.
Weiterhin wurden zwei Kältemaschinen auf eine trockene Rückkühlung des Sekundärkreises und auf eine freie Kühlung des Primärkreises umgestellt. Somit konnte die elektrische Leistung eines Kühlturms eingespart und die hygienische Gefahr der Legionellenbildung umgangen werden. Die freie Kühlung machte eine Erzeugung des Kaltwassers ab einer Außentemperatur von 10°C möglich. Durch den Jahrestemperaturverlauf auf der schwäbischen Alb können heute in fünf von zwölf Monaten die beiden Kältemaschinen außer Betrieb genommen werden.
Weiter ging es 2015 mit der Untersuchung der Heiß- und Kaltwassernetze auf unnötige Leitungswiderstände und einheitliche Temperaturniveaus. Infolgedessen wurden die Leitungsnetze begradigt und die Heizungsverteilungen zweier Heizzentralen mit 3.500 kW Gesamtleistung komplett erneuert. Durch den Einsatz von drehzahlgeregelten Heizungs- und Kaltwasserpumpen konnte auch hier eine deutliche Einsparung an elektrischer Energie erzielt werden. Im Folgejahr wurden vier weitere Kaltwassererzeuger aufgrund ihres Alters und Zustands ausgetauscht. Auch hier wurde auf trockene Rückkühlung des Sekundär- und freie Kühlung des Primärkreises gesetzt.
Weiterhin wurde 2016 in eine neue Drucklufterzeugung investiert. Es wurden insgesamt fünf Drucklufterzeuger außer Betrieb genommen und durch einen drehzahlgeregelten Grundlastkompressor und einen Spitzenlastkompressor ersetzt. Die Kompressoren werden durch Kaltwasser gekühlt. Da ein Anschluss an das Heizungsnetz zur Wärmerückgewinnung aus baulichen und somit ökonomischen Gründen nicht möglich war, wird die erzeugte Wärme ganzjährig über einen Freikühler rückgekühlt. Somit konnte hier auf die Rückkühlung durch eine elektrisch betriebene Kältemaschine verzichtet werden. Schon damals war zu bedenken, dass durch ein BHKW ein sehr viel höheres Temperaturniveau des Heizungswassers erreicht werden konnte und es bei einer möglichen Einspeisung des Rücklaufs der Kompressoren in den geplanten Pufferspeicher eher zu einer Kühlung als zu einer Erwärmung kommen würde.
Parallel wurde die Möglichkeit genutzt, alle Verbraucher zu vernetzen. Somit konnte das Unternehmen 2017 ein Lastgangmanagement installieren. Dies macht ein kontrolliertes Abschalten der Verbraucher der technischen Gebäudeausrüstung möglich. Weiterhin wurden in diesem Jahr die Planungen für das KWKK-Konzept abgeschlossen und eine Kooperation „Virtuelles Kraftwerk Neckar Alb“ eingegangen. Hier ist das Unternehmen an einem Pilotprojekt in Zusammenarbeit mit der Hochschule Reutlingen beteiligt. Das virtuelle Kraftwerk Neckar Alb verfolgt das Ziel, alle relevanten Akteure: Erzeuger, Händler, Verbraucher und Netzbetreiber in einen Querverbund des Strom- und Wärmemarkts einzubeziehen. Somit können sich für Unternehmen als Erzeuger von Energie neue Geschäftsmodelle auftun. Unternehmen können in dieser Zukunftsstudie Energieüberschüsse gegenseitig austauschen und vermarkten.
Damit wurden bereits die Voraussetzungen für die zweite Phase der Maßnahmenumsetzung geschaffen, die 2018 mit der Umsetzung des KWKK-Konzepts beginnen soll. Das Projekt beinhaltet den Leitungsbau, das BHKW, den Absorber sowie einen Pufferspeicher für Wärme. Die Durchführung der Projekte fand in Zusammenarbeit mit der Firma Reuko Klimatechnik mit Sitz in Nagold und der Firma Kunst Drucklufttechnik in Erbach statt.
Im angegebenen Zeitraum wurde eine Summe von mehreren Millionen Euro in die Sanierung der technischen Gebäudeausrüstung investiert. Bis heute wurde der jährliche Verbrauch an elektrischer Energie um 24 % bezogen auf das Ausgangsjahr 2013 gesenkt. Das entspricht rund 4.400 MWh mit einem monetären Gegenwert von ca. 650.000 Euro. Weiterhin werden dadurch jährlich 1.135 t CO2 vermieden.
Die Senkung der Nebenkosten kann in wirtschaftlich kritischen Situationen ein ausschlaggebender Wettbewerbsvorteil sein. Die umgesetzten Maßnahmen waren notwendig, um für die zukünftigen Entwicklungen des Energiemarkts gewappnet zu sein. Das anstehende KWKK-Konzept, das Lastgangmanagement und die Vernetzung der Anlagen (produktiv wie auch unproduktiv) können ein Vorteil bei zukünftig möglichen neuen Arten der Energieversorgung sein. Daher wird auch weiterhin versucht, den Wettbewerbsfaktor Energieverbrauch zu optimieren.
Mayer & Cie. bedient sowohl das obere als auch das mittlere Marktsegment. Insgesamt machten sich im Jahr 2016 rund 1.500 Rundstrickmaschinen auf den Weg zu ihren Kunden auf allen fünf Kontinenten. Die größten Einzelmärkte sind seit Jahren China, die Türkei und Indien. In China hat Mayer & Cie. ein eigenes Tochterunternehmen, in der Tschechischen Republik ein zweites. An beiden Standorten werden einzelne Maschinenlinien endmontiert. Vertriebs- und Serviceniederlassungen von Mayer & Cie. sind in mehr als 80 Ländern präsent. Der Umsatz über die gesamte Unternehmensgruppe betrug im Jahr 2016 105 Mio. Euro, rund 10 % mehr als im Jahr davor. Seit Jahren kann Mayer & Cie. seinen Jahresumsatz kontinuierlich um jeweils 5 bis 10 % steigern. Mit dem Umsatz wächst auch die Anzahl der Mitarbeiterinnen und Mitarbeiter. Am Stammsitz in Albstadt-Tailfingen kommen rund 370 Menschen täglich zur Arbeit. Über die gesamte Gruppe liegt die Zahl der Beschäftigten bei etwa 500. Im Winter 2016/17 machten 22 junge Menschen eine Ausbildung bei Mayer & Cie. in Albstadt. Dabei ist die Chance groß, dass viele über ihre Ausbildung hinaus im Unternehmen bleiben werden. Denn 58 % aller Mayer & Cie.-Mitarbeiter sind seit mindestens zehn Jahren beim Unternehmen, 45 % sogar länger als 20 Jahre.

- Kleinserienfertigung
- Unterstützungsprozesse / Gebäudemanagement
- GreenTech BW ,
- Energiekonzept ,
- Dämmung / Isolation
- Energie ,
- Abgas
- taktisch (1 bis 5 Jahre)