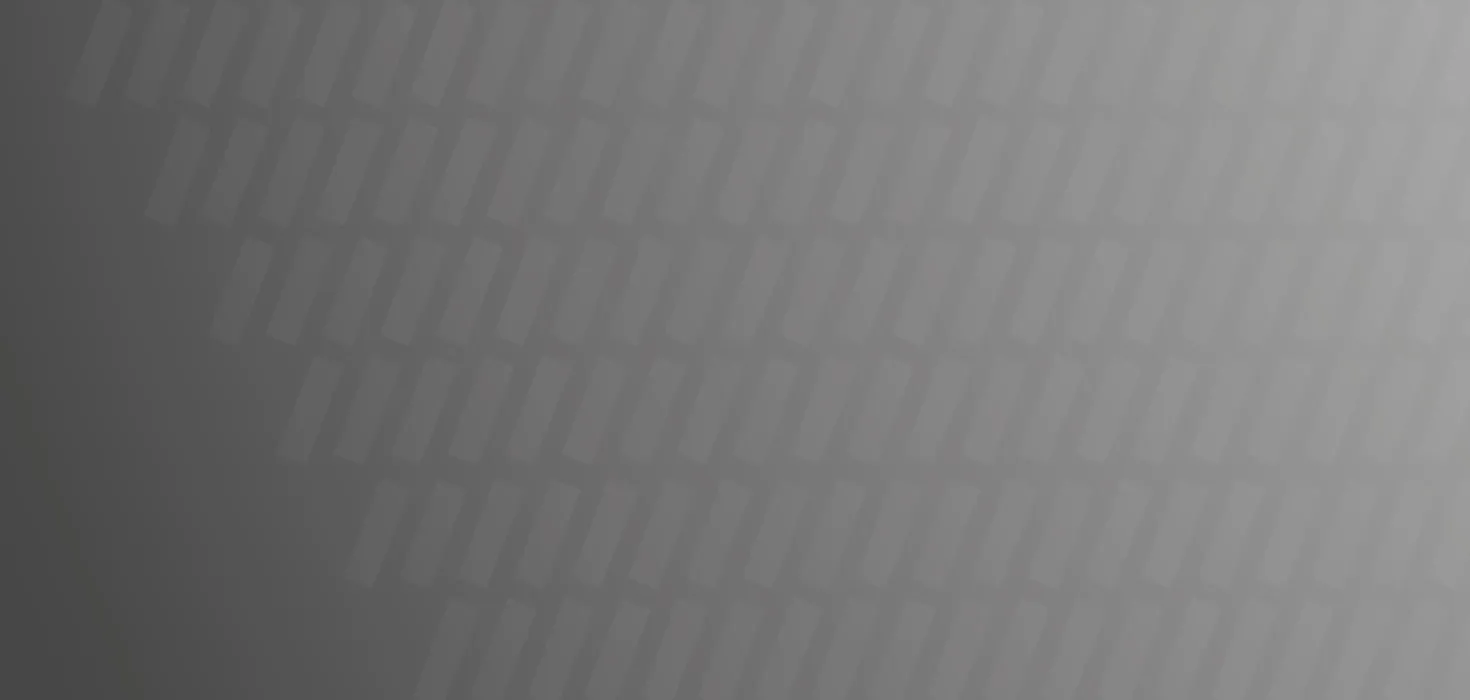
Ressourceneffizienz durch Rückführung von Schmierstoffen
Schmierstoffeinsparung
CO2-Einsparung
Die ABB STOTZ-KONTAKT GmbH entwickelt, produziert und vertreibt innovative Produkte aus dem Bereich der Niederspannungstechnik. Beim Einsatz eines Hochdruck-Dauerschmiersystems kommt es zu einem hohen Verbrauch von Schmiermitteln. Um diesen zu reduzieren, wurde ein System entwickelt, die Schmiermittel in einen Kreislauf einzubauen und somit die Ressourceneffizienz zu erhöhen.
Kostenvorteile
ca. 64.000 Euro
Am Standort Heidelberg produziert ABB STOTZ-KONTAKT Leitungsschutzschalter in einer hochautomatisierten Fertigung. In der Vorfertigung wird unter anderem für diese Geräte das Bauteil „Rahmen“ hergestellt. Dieses Bauteil ermöglicht bei der Verdrahtung einer elektrotechnischen Anlage den Anschluss des Geräts. Im stanz-biegetechnischen Herstellungsprozess erfolgt die Bearbeitung von Bandmaterial aus Stahl in sechs Arbeitsschritten: Stanzen, Biegen, Prägen, Schweißen, Kalibrieren und Gewindeformen. Im letzten Bearbeitungsschritt, dem Gewindeformen, liegt neben hohen Ansprüchen an Arbeitseffizienz und Qualität das Augenmerk insbesondere darauf, eine möglichst lange Standzeit der eingesetzten Gewindeformwerkzeuge zu realisieren.
Diese hohen Qualitätsansprüche an Festigkeit und Oberflächenstruktur der Gewinde bei längeren Standzeiten der Formwerkzeuge erfordern, dass die Anlagen mit einem Hochdruck-Dauerschmiersystem ausgestattet sind. Das System gewährleistet so zum einen die notwendige Schmierung im Formprozess, zum anderen wird die Verlängerung der Formerstandzeiten durch Kühlung erzielt.
Nachteil des eingesetzten Dauerschmiersystems ist allerdings der Verbrauch an hochwertigem Schmierstoff. Zwar wird der Hauptstrom im Kreislauf der Anlage gefiltert und zurück geführt, dennoch erfolgt, bedingt durch die schöpfende Wirkung der Bauteile, ein Austragen des Schmierstoffs in hohem Maße.
Transportbetriebsmittel und Bauteile unterliegen daher einer starken Verschmutzung und müssen einem separaten Entölungsprozess unterzogen werden. Erhebliche Mengen an Schmierstoff werden in der Folge als Abfall entsorgt; der nun fehlende Schmierstoff muss im System ergänzt werden, um die Funktionalität sicherzustellen.
Eine Lösung zur Reduktion des Schmiermittelverbrauchs durch Rückführung ermöglicht es sowohl die Prozess- und Materialkosten als auch die Umweltauswirkungen zu senken und Bearbeitungszeiten insgesamt zu reduzieren.

Die Rückführung des Schmierstoffs in den Kreislauf erfolgt durch eine anlagen- und teilespezifische Blas-Saugkammer mit nachgeschaltetem Filter. Die konstruktive Integration dieser Lösung in die bestehende Maschine sowie die Einbindung in die existierende Hauptanlagensteuerung erwiesen sich dabei als besondere Herausforderung.
Nach der Konstruktion wurde die Blas-Saugkammer zunächst für eine Pilotierung in einer der drei Anlagen eingesetzt. Sehr schnell zeigte der Praxistest, dass die erwarteten Ergebnisse erzielt werden konnten. Zwei weitere Anlagen wurden daher umgehend mit der Zusatzkonstruktion nachgerüstet.
In jeder der drei Anlagen folgt nun nach dem Gewindeformen ein weiterer Schritt zum Ausblasen des überschüssigen Schmiermittels. Hierbei werden gemäß der Taktzeit immer drei Gewinde, die am Stanzanbindungsstreifen befestigt sind, in der nachgeschalteten neuen Saug-Blaskammer ausgeblasen und mittels Unterdruck abgesaugt. Die Saug-Blaskammer verfügt über mehrere bewegliche Luftdüsen, die so ausgerichtet sind, dass eine maximale Reduktion des Schmiermittels erfolgt.
Der ölhaltige Luftstrom wird dem geschlossenen Rohrsystem einer Abscheideeinrichtung zugeführt. Dort erfolgt durch Zentrifugalkraft die Trennung der Feinöltropfen aus dem Luftstrom. Die so gewonnene Ölmenge fließt in das Filtersystem und folglich in den Gesamtprozess zurück.
Der Einsatz der Blas-Saugkammer zur Ölreduzierung schlägt sich in einer deutlichen Verminderung des eingesetzten Schmierstoffs und des Abfallvolumens nieder. Zudem wurde eine höhere Sauberkeit der Peripherie und Transportbehältern erreicht, der Aufwand für die Entölung konnte deutlich gesenkt werden.
Seit der Einführung der Saug-Blaskammern konnten ca. 18,5 t Schmierstoff eingespart werden, das entspricht einer Einsparung in Höhe von ca. 64.000 Euro. Damit verbunden konnten die CO2-Emissionen um rund 52 t reduziert werden. Diese Ergebnisse unterstreichen die Wirksamkeit der realisierten Lösung.
Bei ABB STOTZ-KONTAKT wurde eine bestehende Technologie an die Gegebenheiten vor Ort angepasst und damit beachtliche Einsparungen erzielt. Technologie und Vorgehen lassen sich einfach auf andere Betriebe und Fertigungen übertragen und kann als Ansatzpunkt dienen, die Ölverschleppungen in verschiedensten Prozessen zu reduzieren.
Die partnerschaftliche Zusammenarbeit zwischen Anlagenherstellern und Betreibern war in diesem Fall auch Erfolgsfaktor für die Identifikation und Umsetzung neuer Lösungsansätze. Der etablierte KVP-Prozess trägt zur nachhaltigen Verfolgung gezielt bei.
Die ABB STOTZ-KONTAKT GmbH entwickelt, produziert und vertreibt innovative Produkte aus dem Bereich der Niederspannungstechnik. Innovative Produkte in Verbindung mit marktgerechten Dienstleistungen unterstützen Kunden aus den verschiedensten Segmenten dabei, einen Nutzen- und Anwendungsvorteil in ihren jeweiligen Anwendungen zu erreichen. ABB STOTZ-KONTAKT ist ein Unternehmen ABB Gruppe.
ABB (www.abb.com) ist ein global führendes Technologieunternehmen in den Bereichen Energie und Automation. Das Unternehmen ermöglicht seinen Kunden in der Energieversorgung und der Industrie ihre Leistungsfähigkeit zu verbessern und gleichzeitig die Umweltbelastung zu reduzieren. Die Unternehmen der ABB-Gruppe sind in rund 100 Ländern tätig und beschäftigen weltweit etwa 135.000 Mitarbeitende.

- Großserienfertigung
- Unterstützungsprozesse / Gebäudemanagement
- GreenTech BW ,
- Stoffkreislauf / Recycling
- Material ,
- Chemieprodukte ,
- Abfälle ,
- Abgas
- operativ (kleiner 1 Jahr)