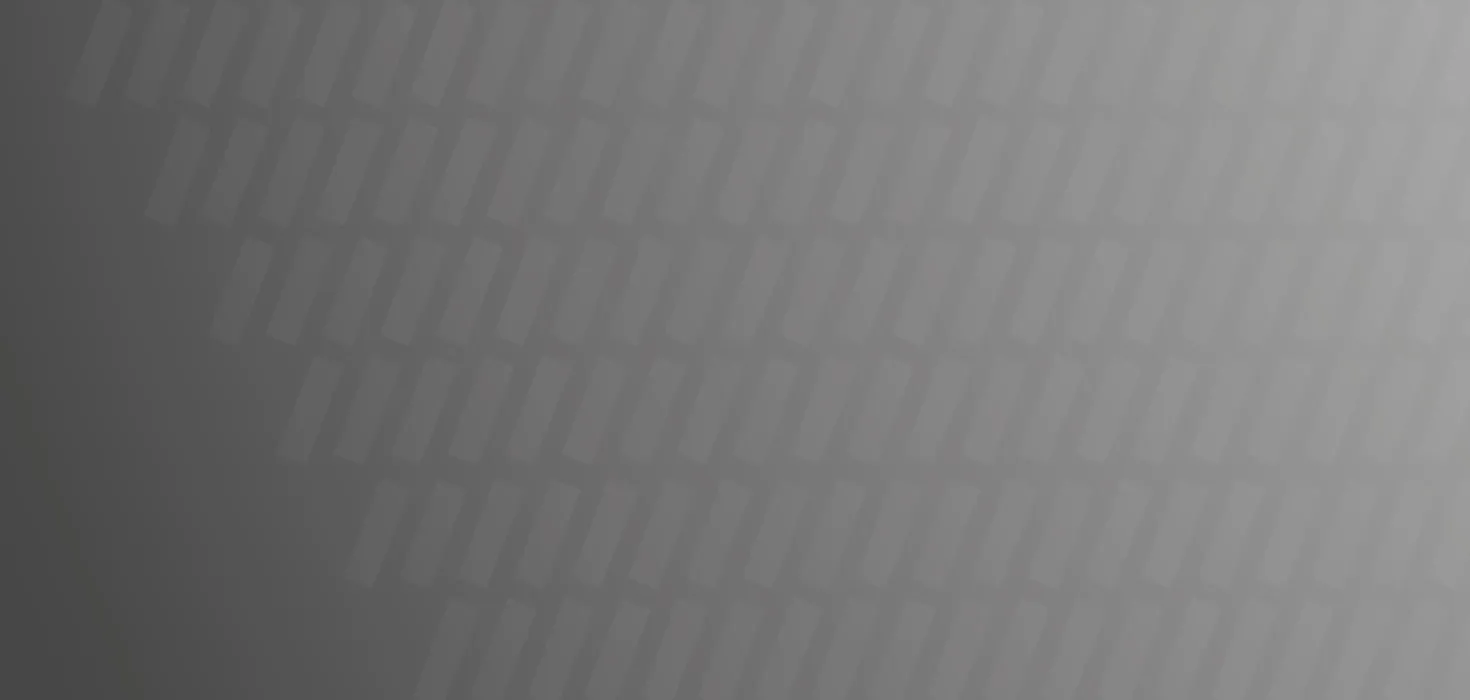
Toleranzausgleichselement: Ressourceneffizienz durch Produktentwicklung
Fe-Metalleinsparung
Transportwegeinsparung
Springfix Befestigungstechnik produziert vor allem Komponenten, die in der Automobilindustrie eingesetzt werden. Durch eine Änderung des Produktdesigns der Toleranzausgleichselemente sollte einige Prozessschritte in deren Produktion sowie den Rohstoffeinsatz reduzieren. Dadurch wird eine ressourcensparende Fertigung bei gleichbleibender Funktionalität und Qualität des Artikels gewährleistet.
Springfix Befestigungstechnik produziert am Standort Salach Komponenten, die vor allem in der Automobilindustrie eingesetzt werden. Ein wichtiges Produkt in diesem Markt sind Toleranzausgleichselemente (TAE). Diese Elemente sind verstellbar und ermöglichen durch Ausdrehen einen Toleranzausgleich zweier Anbauteile bei der Montage eines Kraftfahrzeugs. Es werden dadurch Spaltmaße angepasst und Toleranzschwankungen, bspw. zwischen Scheinwerfer und Karosserie, ausgeglichen. Der geschätzte weltweite Jahresbedarf an Toleranzausgleichselementen liegt derzeit bei rund 12 bis 15 Mio. Stück.
Das Produkt besteht bisher in der Regel aus sieben Einzelteilen, welche bis auf eines aus Stahl gefertigt werden. Fünf der sechs Stahlteile werden vergütet und im Anschluss galvanisch veredelt. Nur durch diese Folgeprozesse können die Anforderungen an Festigkeit und Korrosionsschutz erreicht werden. Ein hoher logistischer und qualitätssichernder Aufwand ist notwendig, um die geforderten Qualitätsansprüche der Kunden zufrieden zu stellen.
Die Zielsetzung war es, eine ressourcensparende Fertigung bei gleichbleibender Funktionalität und Qualität des Artikels zu gewährleisten. Eine Änderung des Produktdesigns sollte Prozessschritte wie Vergüten und Galvanisieren reduzieren oder gar eliminieren sowie Rohstoffe einsparen.
Die Reduktion der Teileanzahl und damit auch der Prozessschritte sollte Material einsparen und Transportwege reduzieren. Darüber hinaus sollte sich somit auch eine Verringerung der Treibhausgasemissionen erwirken lassen. Außerdem sollte die verkürzte Prozesskette das Fehlerpotenzial verringern und damit eine einfachere Qualitätssicherung ermöglichen, so dass auch in diesem Bereich der Aufwand reduziert wird. Fertigfallende Teile sorgen schließlich für eine einfachere Handhabung in Logistik und Qualitätssicherung, sind weniger fehleranfällig und steigern somit den Durchsatz im gesamten Unternehmen.
Zunächst konnten vier Einzelsteile, die beiden Gewindeteile, der Haltering sowie die Anlagefläche Anschlagring, in zwei Kunststoffbauteilen zusammengefasst werden. Anschließend wurde die Funktionalität dieser Materialsubstitution im Rahmen von Belastungstests bestätigt. Dazu wurde insbesondere die Temperatur- und Vibrationsempfindlichkeit der Komponenten getestet. Zudem konnte durch weitere Optimierungen je nach Einsatzgebiet entweder der Z-Clip samt Mutter ersetzt werden oder das Federelement entfallen. Dies führte zu weiteren Material- und Gewichtseinsparungen. Die Anzahl der Einzelteile konnte somit von sieben auf vier reduziert werden. Durch die Neugestaltung der Einzelelemente konnten Prozessschritte und Rohstoffeinsätze reduziert werden. Dies trägt schlussendlich zur Schonung von Ressourcen bei. Gleichzeitig steigert das neue Verfahren die Produktqualität.
Die Materialsubstitution und die konstruktiven Änderungen am Produkt führen insgesamt zu jährlichen Materialeinsparungen in Höhe von 740 t Fe-Metalle. Darüber hinaus entfällt für 115 t Fe-Metalle die Vergütung, d. h. das energieintensive Härten und Anlassen. Für weitere 335 t Fe-Metalle wird die Galvanisierung obsolet. Damit kann auf die dabei eingesetzte elektrische Energie sowie die entsprechenden Materialien der Zink-Nickel-Beschichtungen bzw. die dazu notwendigen Chemikalien verzichtet werden und es werden auch erhebliche Mengen an Abwasser und Galvanikschlamm vermieden. Zudem entfallen 72.528 km Transportwege pro Jahr, da nicht nur Rohstoffanlieferungen eingespart werden, sondern auch die Transporte zur Vergütung und Galvanisierung bei Lohnunternehmen. Dieses globale Einsparpotenzial beruht auf dem derzeit geschätzten weltweiten Bedarf an Toleranzausgleichelementen in Höhe von 12 bis 15 Mio. Stück pro Jahr.
Durch die Materialsubstitution kommt es zwar zu einem erhöhten Einsatz von Hochleistungskunststoffen; die im Unternehmen verarbeitete Menge steigt um 26 t auf zukünftig 150 t pro Jahr. Dies schmälert aber nicht den Erfolg des neuen Designs und der Verfahrensumstellung. Denn zum einen handelt es sich hierbei um das reine Teilegewicht und zum anderen stehen diesem Mehreinsatz die genannten 740 t eingesparten Fe-Metalle gegenüber. Zudem werden durch den geringeren Materialbedarf nicht nur die mit dem Transport verbundenen Emissionen minimiert. Es werden auch erhebliche Mengen an elektrischer Energie für die Materialbearbeitung und damit die entsprechenden Treibhausgasemissionen der Energieerzeugung eingespart. Schließlich kommt die 75-prozentige Gewichtseinsparung bei den neu entwickelten Toleranzausgleichselementen auch in ihrer Anwendung in der Automobilindustrie zum Tragen und hilft somit dabei, das Fahrzeuggewicht zu reduzieren.
Bei Springfix Befestigungstechnik wurde durch konsequente Entwicklungsarbeit ein bestehendes Produkt so weit verändert, dass die Funktion sowie die hohen Qualitätsansprüche erhalten und sogar gesteigert wurden. Gleichwohl ermöglichte das neue Verfahren eine deutliche Ressourceneinsparung. Die aus dem Projekt resultierenden Ergebnisse haben gezeigt, dass es auch an bestehenden Komponenten Verbesserungspotenziale gibt, um Ressourcenschonung weiter voranzutreiben. Es ist daher ein lohnender Aspekt, diese zu betrachten.
Die Springfix Befestigungstechnik GmbH ist seit über 50 Jahren zuverlässiger und innovativer Technologiepartner der Industrie und Teil der M.S. Ambrogio s.p.a. Group, Italien. Springfix hat seinen Schwerpunkt vor allem im Bereich Automotive und entwickelt, produziert und vertreibt in diesem Bereich hochinnovative Befestigungselemente. Durch Innovationskraft und höchste Qualitätsstandards schafft Springfix den entscheidenden Vorsprung.
Das Produktportfolio erstreckt sich von der thermoplastischen Kunststoffverarbeitung, im Bereich 25 bis 1.100 t Schließkraft, über die Stanz-Biegeteilfertigung in Folgeverbundlösungen und Bihler-Technik, bis hin zu vollautomatischen, kundenspezifischen Montagelösungen. Sonderapplikationen, wie Widerstandsschweißen auf Bihler-Stanz-Biegeautomaten, sowie die Zuführung und Montage von Schrauben und Muttern auf Stanz-Biegeteilen und 2K-Kunststoffverarbeitung sind wesentliche Bestandteile der täglichen Arbeit.

- Großserienfertigung
- Entwicklung / Konstruktion ,
- Verarbeitungsprozess
- Produktinnovation
- Energie ,
- Material ,
- Metalle ,
- Chemieprodukte ,
- Abwasser ,
- Abfälle ,
- Abgas
- operativ (kleiner 1 Jahr)