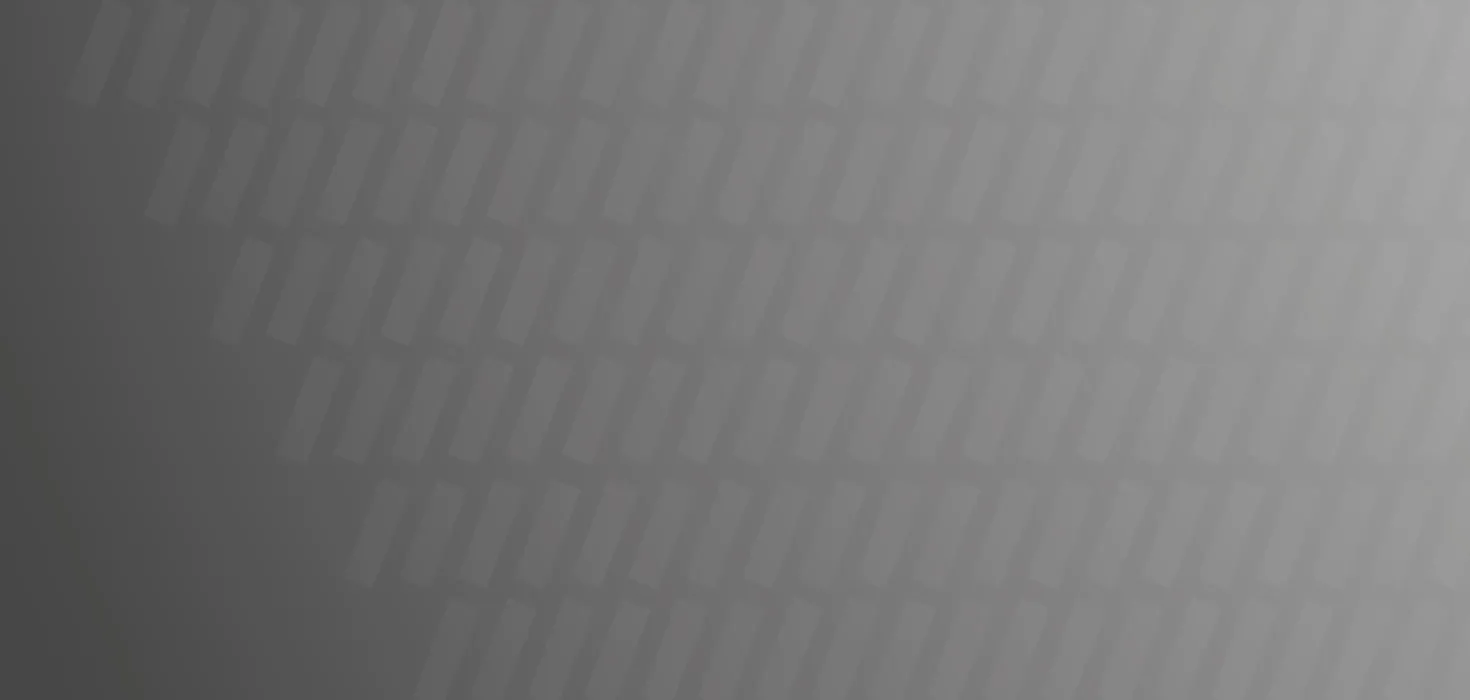
Wärmenutzungskonzept zur Trocknung von Rindenmulch als Brennstoff
Holzspäneeinsparung
Die Finkbeiner KG ist ein Säge- und Hobelwerk aus dem Schwarzwald. Das Heizkraftwerk produziert Strom und Wärme durch die Einspeisung von Sägespänen aus dem Sägewerk. Diese Wärme wurde bisher ungenutzt über die Lüftungsklappen der Gebäude abgeleitet. Das Ziel des Vorhabens war es daher, die Prozessabwärme im Betrieb zu nutzen und dadurch innerbetriebliche Stoff- und Energiekreisläufe zu schließen.
Die Finkbeiner KG betreibt seit vielen Jahren am Standort Steinbis ein Säge- und Hobelwerk. Dort werden ca. 180.000 Festmeter Holz pro Jahr, das sind etwa 30 Lkw-Ladungen pro Tag, verarbeitet. Im Jahr 2015 wurde ein Heizkraftwerk in Betrieb genommen. Das Heizkraftwerk wird mit Spänen aus dem Sägewerk gespeist und liefert bis zu 1,4 MW elektrische Leistung. Der produzierte Strom wird ins Netz eingespeist.
Das Heizkraftwerk produziert neben Strom eine Wärmemenge von ca. 6,8 MW. Diese wird in zehn Trockenkammern mit einer Kapazität von 600 m³ genutzt, in denen auftragsbezogen das selbst produzierte sowie fremdes Schnittholz getrocknet wird. Durch den Prozess wird innerhalb des Gebäudes eine erhebliche Menge an Wärme frei, welche über Lüftungsklappen bislang ungenutzt abgeleitet wird.
Das Ziel des Vorhabens war es daher, die Prozessabwärme im Betrieb zu nutzen und dadurch innerbetriebliche Stoff- und Energiekreisläufe zu schließen. Zunächst wurden im Rahmen der Einfahrphase des Heizkraftwerks die erforderlichen peripheren Energieverbräuche bei verschiedenen Auslastungsgraden gemessen. Hierbei wurde festgestellt, dass bis zu einer Auslastung von ca. 70 % die peripheren Energieverbräuche bei anteilig 3 % liegen. Bei einem Auslastungsgrad von über 70 % steigen hingegen die peripheren Energieverbräuche schnell auf über 6 %.
Somit erzeugt die Anlage bei einem Auslastungsgrad bis 70 % einen Wärmeüberschuss, der durch die Trockenkammern nicht abgenommen werden kann.
Temperaturmessungen haben ergeben, dass im Heizkraftwerksgebäude ständig Lufttemperaturen von mindestens 45 °C vorherrschen. Dementsprechend sollten Maßnahmen ergriffen werden, die der Nutzung der überschüssigen Prozesswärme und der Optimierung des Heizkraftwerks dienen.
Bei einem Rindenanteil in Höhe von ca. 10 % je Festmeter Holz fallen im Säge- und Hobelwerk erhebliche Mengen an Rindenmulch an. Rindenmulch hat allerdings einen Wassergehalt von bis zu 80 % und ist gemeinhin als Brennstoff wegen massiver Versottungsgefahr nicht nutzbar. Die Nutzung von Rindenmulch als Brennstoff ist erst ab weniger als 55 % Restfeuchte möglich. Daher bietet es sich an, die ungenutzte Restwärme aus dem Heizkraftwerksraum, die 15.724,4 MWh/Jahr umfasst, und den Wärmeüberschuss aus dem Heizkraftwerksprozess, der 20.095 MWh/Jahr beträgt, zur Vortrocknung des Rindenmulchs einzusetzen, um diesen anschließend thermisch verwerten zu können.
Zur Umsetzung der Idee wurden einige Umbaumaßnahmen vorgenommen. So wurden ein Absaugventilator und ein Wärmetauscher installiert. Mittels Ventilator wird die ungenutzte Prozesswärme mit einer Temperatur von ca. 40 bis 50 °C aus dem Gebäude abgesaugt und über den Wärmetauscher im Zuluftkanal auf ca. 80 °C nacherhitzt. Der Wärmetauscher wird durch überschüssige Prozesswärme gespeist. Damit steht heiße, trockene Luft aus Wärmeüberschuss technisch zur Vortrocknung des Rindenmulchs zur Verfügung.
Das Heizkraftwerk umfasst Spänebunker mit je 400 m³ Fassungsvermögen. Unterhalb dieser Spänebunker befindet sich eine Halle für den Maschinenpark. An der Decke dieser Halle und unterhalb der Spänebunker wurde ein Zwischenboden aus Stahlblech eingezogen und somit ein Strömungskanal erstellt. Der Austritt aus diesem Strömungskanal erfolgt durch jeweils 24 Bodenlöcher mit Gitterabdeckung (Durchmesser ca. 800 mm). Bei der Planung und Umsetzung der Maßnahme wurde die Finkbeiner KG maßgeblich durch die Energiewelt-info GmbH aus Bad Mergentheim unterstützt.
Der beim Verarbeitungsprozess anfallende Rindenmulch wird innerhalb von sechs Tagen auf 15 bis 20 % Restfeuchte getrocknet. Dies kann alternierend in den Bunkern erfolgen, aber auch gleichzeitig, weil genügend Lagerflächen zur Verfügung stehen. Somit steht Brennmaterial mit einem Wärmepotenzial von 32.524 MWh/Jahr zur Verfügung. Dies ersetzt ca. 25 % des aus Holzspänen bestehenden ursprünglichen Brennmaterials.
Die Späne- bzw. Mulchbunkertrocknung ist so leistungsfähig, dass nach ersten Tests neben der Trocknung von Material aus der eigenen Verarbeitung auch Fremdmaterial eingesetzt werden kann. Eine Vortrocknung von feuchtem Brennmaterial mit nicht genutzter Prozesswärme aus Heizkraftwerken oder auch Blockheizkraftwerken steigert den Brennwert des Materials und nutzt den Prozess optimal aus.
Durch die Abwärmenutzung zur Rindenmulchtrocknung ergeben sich letztlich weitere Effekte auf die Stoffströme im Betrieb. Bisher wurde der anfallende Rindenmulch lediglich mit geringerer Wertschöpfung als Dünger bzw. zur Unkrautverhinderung im Garten- und Landschaftsbau eingesetzt. Durch die thermische Verwertung des Rindenmulchs im Heizkraftwerk werden jedoch dort Holzspäne als Brennstoff substituiert. Die eingesparten Holzspäne, ca. 10.240 t/Jahr, können nun wiederum höherwertig bei der Herstellung von Spanplatten in der Dämmstoff- und in der Möbelindustrie eingesetzt werden.
Die Maßnahmen optimieren und kombinieren die Kraft-Wärme-Kopplung mit dem gesamten Prozessablauf einer Produktion. Dabei muss zur Optimierung der Produktion und Vermeidung von Emissionen ein komplexer Abwägungsprozess von Parametern durchgeführt werden. In der Prozessoptimierung liegt noch ein weiteres Potenzial in Höhe von ca. 3.000 MWh/Jahr, das noch gehoben werden muss.
Aus standardisierten, solitären Einzelprozessen wird aufgrund der Analyse von Stoff- und Energieströmen ein komplexes Abbild geschaffen, um Optimierungshebel anzusetzen. Diese umfassen aus energetischer Sicht in Verbindung mit der Produktion folgende Betriebsbereiche: Entrindung, Sägewerk, Trockenkammern, Heizkraftwerk und vollständige Verwertung von Rohstoffen.
Das Projekt zeigt die Potenziale und Möglichkeiten bei ganzheitlicher Energiebetrachtung eines Unternehmens auf. Es zeigt spezifisch für die Sägewerksbranche, welche energetischen Einsparpotenziale vorliegen und genutzt werden können. Das Projekt ist aber auch beispielhaft auf Heizkraftwerke und auf Blockheizkraftwerke übertragbar.
Die „Steinbissäge“ hat ihren Ursprung im Gutachtal/Schwarzwald vor mehr als 300 Jahren. Seit dem Jahr 1922 betreibt die Familie Finkbeiner in nunmehr fünfter Generation das Säge- und Hobelwerk.
Das Sägewerk bezieht Rundholz aus den Wäldern im Umkreis von 80 km. Eine Vielzahl von regionalen Waldbesitzern liefert jährlich bis zu 200.000 Festmeter Fichten- und Tannenrundholz. Langfristige und faire Partnerschaften mit Lieferanten und Kunden sind die Grundlage der guten Entwicklung der Finkbeiner KG in den vergangenen Jahrzehnten.
Die Qualität der vielfältigen Produkte liegt auf höchstem Niveau, wobei schon seit Jahren auf nachhaltige Waldwirtschaft gemäß der PEFC-Zertifizierung geachtet wird. Aus einem großen Rundholzvorrat können die passende Stärkeklasse und Qualität schnell ausgesucht und die bestellten Hölzer umgehend produziert werden. Diesen Service und die gleichbleibende Qualität schätzen Kunden in ganz Europa.
Die Finkbeiner KG hat sich in den letzten Jahren zum größten Sägewerk im Schwarzwald-Baar-Kreis entwickelt und beschäftigt über 70 Mitarbeiterinnen und Mitarbeiter. Um den hohen Qualitätsstandard unserer Produkte zu halten und stetig auszubauen, werden in dem modernen Betrieb junge Menschen zu qualifizierten Fachkräften ausgebildet.
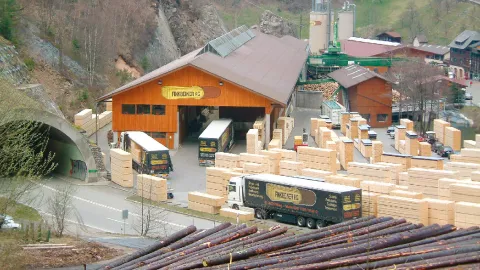
- Kleinserienfertigung ,
- Großserienfertigung
- Unterstützungsprozesse / Gebäudemanagement
- GreenTech BW ,
- Energiekonzept ,
- Stoffkreislauf / Recycling
- Energie ,
- Material ,
- Holz, Karton und Papier ,
- Abgas
- taktisch (1 bis 5 Jahre)