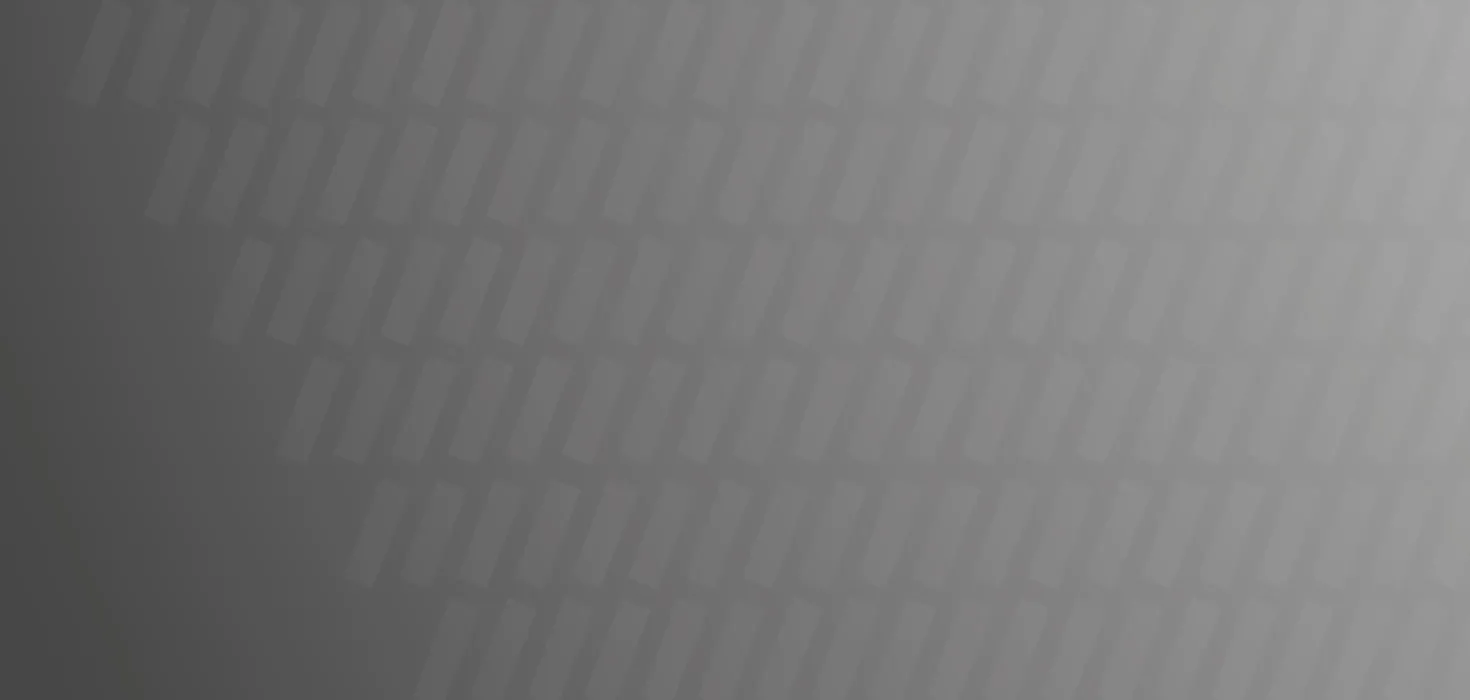
Ätzmittelrecycling und Kupferrückgewinnung in einer alkalischen Ätzlinie
Ätzmittelrückgewinnung
Kupferrückgewinnung
Die Würth Elektronik Gruppe beschäftigt sich unter anderem mit der Herstellung von Leiterplatten. Der Prozess ist sehr komplex umfasst sehr viele Schritte. Einer davon ist die Ätzlinie, die in diesem Projekt neu gestaltet werden sollte. Besonders der Energie- und Wasseraufwand konnte optimiert werden und durch eine anschließende Recyclinganlage wird Ätzmittel und Kupfer zurückgewonnen.
Kostenvorteile
54%ige Senkung der Ätzprozessgesamtkosten pro Quadratmeter
Die Würth Elektronik Unternehmensgruppe mit Stammsitz in Niedernhall (Hohenlohe) umfasst drei Unternehmensbereiche. Der Unternehmensbereich Würth Elektronik Circuit Board Technology (CBT) hat sich als einer der führenden Leiterplattenhersteller Deutschlands etabliert. Das Produktportfolio reicht von Mustern und Prototypen über mittlere Serien bis hin zu großen Volumina. Aus einer Hand finden Elektronikentwickler alle gängigen sowie viele innovative Leiterplattentechnologien bis hin zu Systemlösungen. Täglich passieren über 120 neue Leiterplattendesigns die Fertigungen.
Die Leiterplattenfertigung ist äußerst komplex. Je nach Ausführung durchläuft die Herstellung einer Leiterplatte 72 bis über 130 Einzelprozessschritte. Dabei stellen mehr als die Hälfte chemische Nassprozesse dar, wie beispielsweise Reinigen, Ätzen und Galvanisieren. Ganz konkret sind in der alkalischen Ätzlinie drei Prozesse vereint. Der erste Prozessschritt in der Ätzlinie ist das Entfernen des Galvanoresists. Im darauffolgenden zweiten Prozessschritt, dem eigentlichen alkalischen Ätzprozess, werden die nicht mit Zinn bedeckten Kupferbereiche entfernt. Als dritter Prozessschritt wird beim Zinnstrippen die als Ätzschutz aufgebrachte Zinnschicht entfernt.
Die alkalische Ätzlinie war bei Würth Elektronik in Niedernhall bereits 17 Jahre alt und erfüllte nicht mehr die technischen Anforderungen des Marktes hinsichtlich Ätzgenauigkeit. Daher wurden die Investition in eine neue zukunftsfähige Ätzlinie und der damit verbundene Aufbau geplant.
Technologieseitig wurden folgende Ziele formuliert:
- Sichere Produktion von Strukturen kleiner als 100 µm
- Erhöhung der Ätzgenauigkeit
- Verbesserung der Fertigungsqualität
- Verringerung des Wasserverbrauchs und der Energiekosten
- Steigerung der Kapazität um 50 %
- Reduktion des Analyseaufwands
- Installation von Kupferrückgewinnung und Ätzmittelrecycling
Die Ätzmodule sollten nach dem aktuellen Stand der Technik mit zuschaltbaren Düsenstöcken und partiell wirkendem Nachätzer konstruiert werden. Um den Wasserverbrauch zu senken, sollten Vier- bis Fünffach-Kaskaden mit Leitwertregelung eingesetzt werden. Statt der üblichen Elektroheizung sollte mit Warmwasser geheizt und damit die Abwärme der Druckluftkompressoren genutzt werden. Um wertvolle Produktionsfläche einzusparen, sollte die Recyclinganlage auf einer Stahlbühne über der Produktionslinie installiert werden.
Für den Neubau der Ätzlinie wurden fünf potenzielle Lieferanten angefragt. Vier davon erfüllten die Anforderungen an die neue Linie jedoch nicht. Schließlich lieferte die Gebr. SCHMID GmbH aus Freudenstadt die Ätzlinie und die Schwedische Firma Sigma die Recyclinganlage. Seitens des Unternehmens waren Mitarbeiter der Werkzeuginstandsetzung und der Qualitätssicherung beteiligt. Der Vorteil des Recyclingverfahrens „MECER“ der Firma Sigma war, dass es im Gegensatz zu anderen Verfahren Elektrolytkupfer erzeugt. Dieses kann zu einem hohen Preis wieder verkauft werden. Zur Verringerung des Analyseaufwands wurde Messtechnik für die Größen Leitwert, pH-Wert, Dichte und Redoxpotenzial installiert. Im Jahr 2012 wurde die neue Ätzlinie in Betrieb genommen.

Der Analyseaufwand wurde durch die bedarfsgerechte Prozessregelung über physikalische Messgrößen von einmal pro Schicht auf zweimal pro Woche minimiert. Mittels Ätzmittelrecycling mit Kupferrückgewinnung nach dem MECER-Verfahren, das eine Kombination von flüssig-flüssig Extraktion und Elektrolyse ist, werden über 90 % des Ätzmittels und über 99 % des in der Ätzlösung enthaltenen Kupfers zurückgewonnen. Durch die Nutzung von Abwärme aus den Druckluftkompressoren für die Beheizung der Elektrolyte wurden die Energiekosten halbiert. Die Einsparung im Stromverbrauch betrug 2013 mehr als 250 MWh. Die Gesamtkosten der Ätzprozesse pro Quadratmeter wurden sogar um 54 % gesenkt. Die Recyclinganlage hat sich so in ca. 1,5 Jahren amortisiert.
Der Aufbau der neuen Ätzlinie hat gezeigt, dass optimale Ergebnisse erreicht werden können, wenn man sich Zeit für die Qualifikation lassen kann. Nach dem Großbrand Ende 2014, bei dem ein Großteil der Leiterplattenfertigung zerstört wurde, legte Würth Elektronik den Fokus beim Wiederaufbau auf Automatisierung, Nachhaltigkeit und Wirtschaftlichkeit. Zielsetzung war die Halbierung der Energie- und Wassermengen im Vergleich zur alten Fertigung. Die Erfahrungen aus der Installation der Ätzlinie, die vom Brand nicht betroffen war, konnten hier geschickt ein fließen. So wurden auch in den elf neuen Prozesslinien alle technischen Besonderheiten und Merkmale der Ätzlinie, wie beispielsweise Leitwertregelungen in Spülkaskaden, Warmwasserheizung und mehr, verwendet.
Das neuartige Kupferrecycling lief von Anfang an problemlos und mit wenig Wartungsaufwand. Hierbei wurden die erwarteten Ergebnisse sogar übertroffen. Auf Basis dieser Erkenntnisse und des Erfolgs soll nun auch im Werk Schopfheim ein Kupferrecycling aufgebaut werden. Außerdem wird untersucht, ob das zurückgewonnene Kupfer im geschlossenen Kreislauf direkt wieder in der eigenen Produktion eingesetzt werden kann.
Die Würth-Gruppe ist Weltmarktführer in ihrem Kerngeschäft, dem Handel mit Montage- und Befestigungsmaterial. Sie besteht aktuell aus über 400 Gesellschaften in mehr als 80 Ländern und beschäftigt über 73.000 Mitarbeiterinnen und Mitarbeiter. Im ersten Halbjahr des Geschäftsjahres 2017 erzielte die Würth-Gruppe einen Umsatz von 6,4 Mrd. Euro. Die Würth Elektronik Unternehmensgruppe mit ihrem Stammsitz in Niedernhall (Hohenlohe) beschäftigt weltweit rund 8.000 Mitarbeiterinnen und Mitarbeiter und erwirtschaftete im Jahr 2016 einen Umsatz von 785 Mio. Euro. Mit weltweit 16 Produktionsstandorten gehört Würth Elektronik zu den erfolgreichsten Gesellschaften der Würth-Gruppe. Würth Elektronik ist mit drei Unternehmensbereichen auf verschiedenen Märkten international aktiv: Elektronische & Elektromechanische Bauelemente, Leiterplatten und Intelligente Power- und Steuerungssysteme.
- Großserienfertigung
- Entsorgung / Recycling
- GreenTech BW ,
- Energiekonzept ,
- Prozessoptimierung ,
- Stoffkreislauf / Recycling
- Energie ,
- Material ,
- Trinkwasser ,
- Metalle ,
- Chemieprodukte ,
- Abwasser ,
- Abgas
- taktisch (1 bis 5 Jahre)