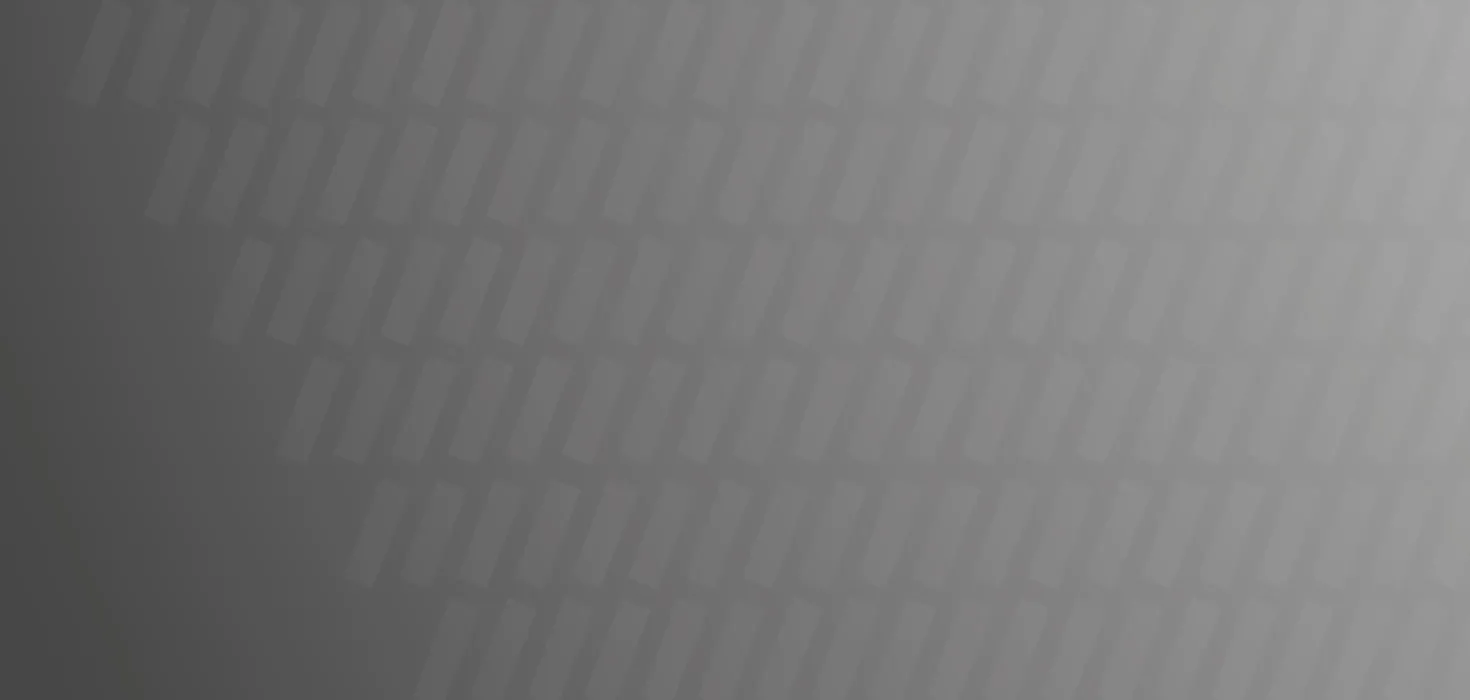
Durch MFCA zu höherer Ressourceneffizienz in der Apfelessigherstellung
Apfelweineinsparung
Verringerung der Ethanolemissionen
Die Friedrich Feldmann GmbH ist ein Produzent von Apfelessig und Lieferant vieler Handelsunternehmen. Das Unternehmen wollte im Hinblick auf seine Kosten, aber auch den immer präsenteren Nachhaltigkeitsgedanken, seine Ressourceneffizienz verbessern. Darum hat das Unternehmen einen Kondensator am Gärtank installiert, um den Verlust des Alkohols über die Abluft zu reduzieren.
Kostenvorteile
11.000 EUR/a durch geringeren Rohstoffeinsatz
Investition
16.000 EUR Anlagenmodifikation
Die Friedrich Feldmann GmbH & Co. KG produziert sowohl Gärungsessig als auch Apfelessig und ist Lieferant vieler Handelsunternehmen. Im Lebensmittelhandel führen kleine Gewinnspannen zu einem relativ hohen Kostendruck auf die Hersteller. Gleichzeitig bildet sich sowohl bei Verbrauchern als auch im Unternehmen ein wachsendes Bewusstsein für eine nachhaltige Nutzung natürlicher Ressourcen aus. Diese beiden Umstände führen dazu, dass ein sparsamer Umgang mit Ressourcen für das Unternehmen, sowohl aus Kostensicht als auch im Hinblick auf die Umweltbilanz seiner Produkte, von großer Bedeutung ist.
Die höchsten Ressourcenverluste wurden im Vorfeld des Projekts vor allem in der Herstellung vermutet. Hier war bekannt, dass ein Teil des eingesetzten Apfelweins während des Prozesses verloren geht. Ziel des Projekts war es, den Ursprung und die Höhe dieses und anderer Verluste aufzudecken und Maßnahmen abzuleiten, um diese Verluste zu verringern oder gänzlich zu vermeiden.
Um Erkenntnisse zu erhalten, wie hoch die Materialverluste an verschiedenen Prozessstellen tatsächlich sind und welchen monetären Wert sie haben, sollte eine Materialflusskostenrechnung (Material Flow Cost Accounting, MFCA) auf die Essigherstellung angewendet werden. Dabei handelt es sich um ein ISO-normiertes Managementinstrument, das darauf abzielt, die durch Ineffizienzen im Produktionsprozess vernichtete Wertschöpfung offenzulegen. Die Verluste werden dabei sowohl in physischen als auch monetären Einheiten erfasst und bewertet. Es ist darüber hinaus möglich, die Verluste mit CO2-Äquivalenten zu bewerten, um so deren Auswirkungen auf die Umwelt zu erfassen. Die MFCA sollte im Unternehmen im Rahmen einer studentischen Abschlussarbeit erfolgen.
Die Ergebnisse zeigten, dass während des Gärungsprozesses im Gärtank, auch Acetator genannt, ein Teil des Alkohols über die Abluft verloren ging. Um diesen Verlust zu minimieren, sollte auf dem Dach des Acetators ein Kondensator installiert werden, welcher den flüchtigen Alkohol durch das Herunterkühlen der Abluft in die flüssige Phase übertreten lässt und direkt in den Tank zurückführt.
In Zusammenarbeit mit der Produktionsleitung wurden alle Material- und Energieströme des Produktionssystems Essigherstellung erfasst. Dazu wurde die vom Land Baden-Württemberg zur Verfügung gestellte Software bw!MFCA eingesetzt. Diese Software ist für die Modellierung, das Verständnis und die Analyse des Produktionssystems überaus hilfreich.
Dabei ergab sich unter anderem, dass der Alkoholverlust vor allem auf den Gärprozess zurückzuführen war. Bedingt durch die exotherme Reaktion der Essiggärung und die Temperatursensibilität der Essigbakterien werden die Gärgeräte zwar gekühlt, jedoch reicht diese Temperatur nicht aus, um ein Verdampfen des eingesetzten Alkohols auszuschließen. Folglich gingen beachtliche Mengen an verflüchtigtem Alkohol über die Abluft verloren. Dieser Verlust konnte mithilfe der Stoffstromanalyse genau quantifiziert werden. Im Rahmen der MFCA wurden diesem Verlust nicht nur alle reinen Materialkosten, sondern auch die Kosten der bereits ins Produkt eingegangenen Wertschöpfung wie z. B. Energie und Personal zugerechnet.
Als technische Maßnahme, um den Materialverlust zu verringern, wurde seitens der Produktionsleitung die Installation eines Kondensators veranlasst. Die Kühlung erfolgt dabei durch Wasser, dessen Temperatur mit Hilfe eines installierten Wasserkühlers auf 8 °C herabgesetzt wird.
Durch diese relativ einfache Maßnahme mit einem geringen Investitionsvolumen kann ein großer Teil des flüchtigen Alkohols zurückgeführt werden. Mindestens 60 % des verdampften Rohstoffs werden direkt wieder in den Tank geleitet. Die jährliche Einsparung an Apfelwein beträgt 4,8 % der eingesetzten Menge. Abzüglich der Energiekosten für das Kühlaggregat führt der geringere Rohstoffeinsatz pro Jahr zu einer Ersparnis in Höhe von fast 11.000 Euro. Durch eine Ausdehnung dieser Maßnahme auf weitere Acetatoren, die teilweise ein deutlich größeres Füllvolumen als das Untersuchungsobjekt aufweisen, könnte sich die Ersparnis weiter erhöhen.
Die Investitionskosten für die Maßnahme beliefen sich auf ca. 14.000 Euro für Kondensator, Wasserkühler und die Rahmeninstallation. Die Aufwände für Personal betrugen ca. 2.000 Euro. Dementsprechend wird sich die Maßnahme bereits nach weniger als eineinhalb Jahren amortisiert haben.
Schließlich wurden die Ethanolemissionen um 3.185 kg verringert. Die im Vorfeld während der Alkoholproduktion anfallenden Emissionen, die durch den verminderten Einsatz von Apfelwein vermieden werden können, sind sogar noch höher einzuschätzen.

Das Projekt zeigt, dass sich die systematische Analyse der physischen Stoffströme im Produktionsprozess lohnt, um die Ressourceneffizienz des Betriebs zu steigern. Die verbesserte Datenbasis und die Kenntnis der tatsächlichen Einsparungen potenzieller Maßnahmen im Verhältnis zu deren Investitionskosten beschleunigten den Umsetzungsprozess sowie die betriebsweite Akzeptanz der Maßnahme. In diesem Zusammenhang war die Kommunikation der Ergebnisse an alle involvierten Funktionsbereiche im Unternehmen von hoher Bedeutung.
Durch eine vergleichsweise einfache Lösung können große Mengen eines zentralen Rohstoffinputs eingespart werden. Das Prinzip des Kondensators ließ sich im Anschluss auf alle vergleichbaren Prozesse übertragen. Zusätzlich konnten die Erkenntnisse aus der Stoffstromanalyse auch zu einer verursachungsgerechteren Zuordnung von Kosten im Controlling beitragen. Dementsprechend wurde das Instrument MFCA bereits auf weitere Teile der Produktion angewendet.
Die Friedrich Feldmann GmbH & Co. KG hat sich seit ihrer Gründung im Jahr 1929 auf die Herstellung verschiedener Essigsorten spezialisiert. Im Sortiment finden sich Branntweinessig und Apfelessig, sowohl in konventioneller als auch in Bio-Qualität, Essig-Essenz, Balsamico-Crema und einige weitere Produkte. Den Essig vertreibt das Unternehmen unter der Marke Feldmann und als Partner zahlreicher Handelsmarken. Die eigene PET-Anlage mit einer Stundenleistung von 16.000 Flaschen ermöglicht es Feldmann zudem, den produzierten Essig auch selbst in verschiedenste Behältnissen abzufüllen.
Die Firma gehört seit dem Jahr 2013 zusammen mit der Speyer & Grund GmbH & Co. KG zu einer Unternehmensgruppe und beschäftigt am Standort Karlsruhe 29 Mitarbeiterinnen und Mitarbeiter. Der Umsatz lag im Geschäftsjahr 2015/16 bei rund 10 Mio. Euro.
- Großserienfertigung ,
- Prozessindustrie
- Verarbeitungsprozess
- Prozessoptimierung ,
- Stoffkreislauf / Recycling ,
- Materialflusskostenrechnung MFCA
- Energie ,
- Material ,
- Sonstige Materialien ,
- Abgas
- taktisch (1 bis 5 Jahre)