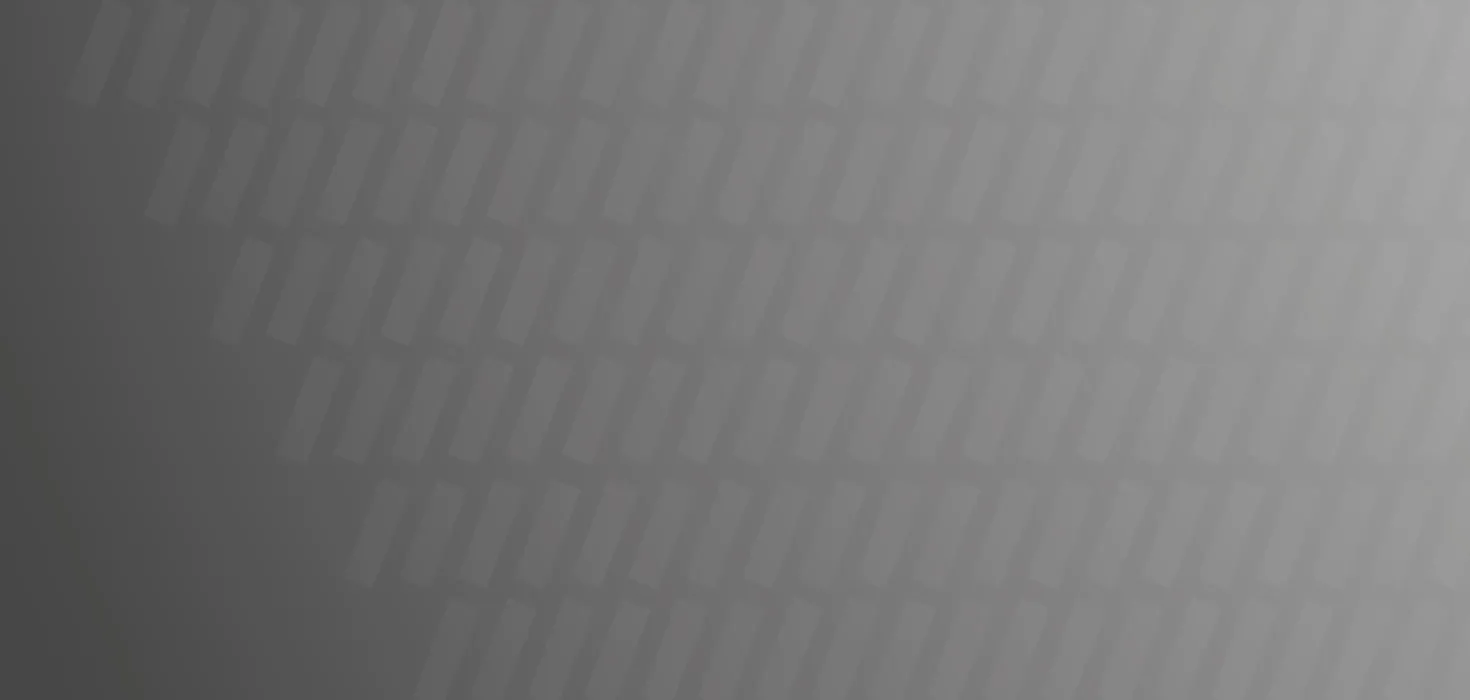
2nd Life Gleisschotter – Nicht(s) für das Abstellgleis!
CO2-Einsparung
Die RUZ Mineralik GmbH bereitet Gleisschotter auf und trägt so zur Kreislaufführung von Baumaterialien bei, die ansonsten deponiert werden müssten. Das Unternehmen erreicht zudem mit einigen Maßnahmen die Steigerung der Ressourceneffizienz, die Optimierung von Betriebsabläufen und das Schließen von Stoffkreisläufen. Der Ansatz des Unternehmens hat zu sehr hohen Ressourceneinsparungen geführt.
Die RUZ Mineralik GmbH aus Heilbronn ist auf die Aufbereitung mineralischer Produkte und Abfälle spezialisiert, um diese anschließend wieder dem Rohstoffkreislauf zuzuführen. Eines dieser Produkte ist Gleisschotter.
Gleisanlagen bestehen aus mehreren Schichten. Die oberste und sichtbare Schicht ist das Schotterbett aus Basalt, einem Hartgestein. Hartgesteinbrüche sind überwiegend in Mitteldeutschland zu finden. Im Gegensatz zu den in Baden-Württemberg angesiedelten Kalksteinbrüchen muss für den Abbau von Hartgestein in tieferliegende Flöze vorgedrungen werden, was einen deutlich höheren Aufwand beim Abbau bedeutet. Entscheidend für das Schotterbett ist die Form der Schottersteine. Diese müssen Bruchkanten aufweisen, damit sie sich verzahnen und ein belastbares und zugleich abfederndes Gefüge entsteht. Zudem ist die Größe der Steine wichtig. Zu kleine Steine würden vom Luftsog der Züge mitgerissen, zu große Steine ließen sich schlecht verarbeiten.
Aufgrund der Belastung durch die Züge nutzt sich der Gleisschotter mit der Zeit ab und verliert seine stützende Funktion, weshalb er regelmäßig ausgetauscht werden muss. Da zur Freihaltung von Bewuchs an Gleisanlagen häufig Pflanzen schutzmittel eingesetzt werden, ist der Schotter damit benetzt. Schwermetall belastungen sind ebenfalls typisch für Gleis schotter. Aus diesem Grund muss der Gleisschotter vor einer Wiederverwendung fachgerecht aufbereitet werden. In Deutschland fallen jährlich über 3,5 Mio. t abgenutzter Gleisschotter an, die ersetzt werden müssen. Aktuell kommen jährlich etwa 0,5 bis 0,7 Mio. t Gleisschotter aus Recyclinganlagen.
Die RUZ Mineralik hat sich bereits seit dem Jahr 2010 der Gleisschotteraufbereitung verschrieben. Die erste Produktionsanlage, bestehend aus vielen einzelnen Produktionsschritten, bildete jedoch keinen durchgängigen Produktionsprozess ab. Dies hatte beschränkte Produktionskapazitäten zu Folge und führte zu ineffizienten Einzelabläufen in der Aufbereitung. Mit zunehmender Erfahrung und stetigen Optimierungen der bestehenden Anlage setzte sich das Unternehmen das Ziel, ein Konzept für eine Aufbereitungsanlage nach neuestem Stand der Technik zu entwickeln und umzusetzen. Die neue Anlage sollte die Leistungsfähigkeit steigern, Frischwasser einsparen und die zu entsorgende Menge an Reststoffen reduzieren.
Für das neue Anlagenkonzept sollten alle Aufbereitungsschritte als zusammenhängendes System gedacht und geplant werden, wodurch es möglich werden sollte, die jährliche Verarbeitungskapazität von etwa 60.000 auf bis zu 250.000 t pro Jahr zu erhöhen. Um dieses Ziel zu erreichen und auch den Einsatz an Material und Energie zu reduzieren, sollte nicht nur der Aufbereitungsprozess nachhaltig gestaltet werden, sondern auch die Anlieferung und Abfuhr des Materials.
Die Entwicklung und Konstruktion der Anlagentechnik erfolgte in enger Zusammenarbeit mit der österreichischen SBM Mineral Processing GmbH. Im Bereich der Wasseraufbereitung kooperierte die RUZ Mineralik mit der schweizerischen Metcam AG und der italienischen Firma Tecnoidea Impianti. Nach erfolgreichem Testbetrieb erfolgte im Sommer 2018 die Abnahme und Inbetriebnahme der Anlage.
Die neue Aufbereitungsanlage zeichnet sich durch einen überwiegend vertikalen Aufbau aus. So wird die Schwerkraft für den Materialtransport durch die verschiedenen Bearbeitungsebenen genutzt, weswegen weniger Förderbänder notwendig sind. Durch die lange Wanne des Schwertwäschers kann die Verweildauer des Materials im Waschbehälter verlängert werden. Dies ergibt bei identischem Durchsatz eine gesteigerte Reinigungsqualität. Zusätzlich wurde eine Hochdruck-Nachspül- Einheit installiert, die alle nach der Schwertwäsche eventuell noch anhaftenden Schmutzpartikel vom Gestein entfernt. An der Nachsortierstation werden vorhandene Störstoffe aus dem Materialstrom entfernt. Aktuell wird dieser Prozess durch eine optische Druckluft-/ Sensorprüfung weiterentwickelt. Ziel ist es, durch die Sensorik den Anteil an Störstoffen maschinell auszusortieren und die Qualität des Recycling-Schotters (RC-Schotter) weiter kontinuierlich zu steigern.
Ein geschlossener Wasserkreislauf mit Wasseraufbereitung und automatisierter Schlammpressung reduziert die final zu entsorgenden Abfallmengen auf das absolut Notwendigste und spart Frischwasser zur Ergänzung des Kreislaufs ein. Die im Wasserkreislauf vorhandene Flockungsmittelkonzentration wird sensorgesteuert erfasst. Die Sensorik steuert durch eine Infrarotsonde das Absetzverhalten des Schlammanteils im Wasser und fügt dementsprechend Flockungsmittel bedarfsgerecht bei, wodurch der Schlammanteil vom Prozesswasser getrennt wird. Für eine tägliche Fertigungsmenge von ca. 700 t werden 25 kg Flockungsmittel benötigt. In der alten Anlage wurden für die gleiche Fertigungsmenge RCSchotter 175 kg Flockungsmittel benötigt. Das eingesetzte Flockungsmittel ist ökologisch abbaubar und wird ebenfalls in der Wasseraufbereitung von Kläranlagen verwendet.
Anstelle der üblichen Metallsiebe kommen Kunststoffsiebe zum Einsatz. Metallsiebe führen zu einer Abrundung der Kanten des Gesteins und haben eine kürzere Lebensdauer, da sie in einem Intervall von vier Wochen ausgetauscht werden müssen. Die Kunststoffsiebe hingegen werden nach etwa einem Jahr ausgetauscht, entsorgt und kreislaufgerecht recycelt.
Eine durchgehend parallele Produktion von RC-Gleisschotter und sämtlichen anderen RC-Körnungen erhöht die Prozesseffizienz durch entfallende Umrüstzeiten und höhere Durchsatzmengen. Aufgrund des beschriebenen Anlagenaufbaus ist im Vergleich zu herkömmlichen Aufbereitungsanlagen auch die Verarbeitung von problematischen Materialien wie Altschotter-Boden-Gemisch oder ähnlichen bindigen Stoffen möglich und garantiert eine hohe Verwertungsquote.
Nach der Realisierung der Aufbereitungsanlage wurden weitere Optimierungsmaßnahmen im Bereich der Materialanlieferung und -abfuhr umgesetzt. So wurde 2021 ein Gleisanschluss auf dem Gelände der Gleisschotterwaschanlage in Betrieb genommen, wodurch Materialanlieferungen und Materialabholungen per Bahn abgewickelt werden können. Dadurch entfällt der bisherige Umschlag auf den Lkw zum Teil sowie die damit verbundenen Emissionen, Verkehrsbelastungen und der Anteil an Leerfahrten. Die Rangierarbeiten an der neuen Gleisanlage erfolgen mit einem elektrisch betriebenen Triebfahrzeug.
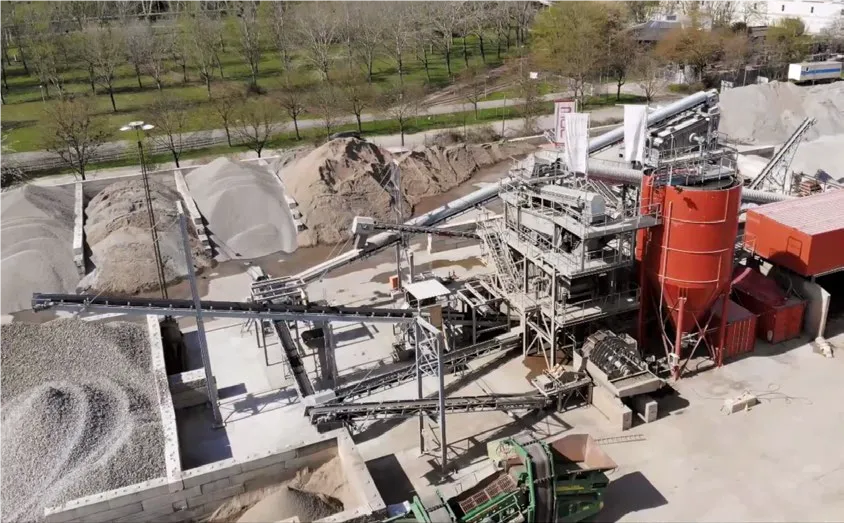
Die RUZ Mineralik verarbeitete 2021 rund 140.000 t Gleisschotter. Daraus entstanden in etwa 49.000 t recycelter Gleisschotter, 46.000 t Splitt in unterschiedlicher Körnung, 6.000 t Brechsand, 11.000 t Waschsand, 7.000 t Filterkuchen und 18.000 t Sonderfraktionen. Je nach Qualität des Eingangsmaterials schwankt die Verwertungsquote zwischen 90 % bis 98 %. Die Gesamtkapazität der Anlage liegt bei ca. 250.000 t jährlich. Für die Aufbereitung des Gleisschotters werden jährlich rund 350 MWh Strom, 320.000 l Wasser und 5 t Flockungsmittel benötigt. Das entspricht CO2-Emissionen in Höhe von rund 218 t CO2e. Gegenüber der alten Anlage werden pro Jahr etwa 206 t CO2e weniger emittiert. Durch den Einsatz des elektrisch betriebenen Triebfahrzeugs werden gegenüber der alten Dieselvariante pro Jahr 0,7 t CO2e vermieden. Bei der Primärgewinnung von 49.000 t Hartgestein für Gleisschotter würden zum Vergleich etwa 772 t CO2e entstehen also etwa 3,5-mal so viel wie beim Recycling.
Durch die Investition in die neue Anlage konnte die Prozessqualität und -effizienz deutlich erhöht werden. Zudem erweitert sie die Flexibilität des Unternehmens hinsichtlich der verarbeitbaren Eingangsmaterialien. Beides trägt zur Steigerung der Wettbewerbsfähigkeit bei. Die enge Zusammenarbeit mit verschiedenen Maschinen- und Anlagenbauern hat ein ausgeklügeltes Anlagenkonzept entstehen lassen und zur erfolgreichen Umsetzung des Vorhabens beigetragen. Darüber hinaus wird auch das bestehende Anlagenkonzept durch weitere Maßnahmen wie z. B. die Druckluft-/Sensorprüfung kontinuierlich weiter optimiert.
Die RUZ Mineralik bildet zusammen mit der Sanierung im Erd- und Rückbau GmbH den Unternehmensverbund SER/RUZ. Bei der RUZ werden mineralische Materialien ressourceneffizient aufgearbeitet, um nach einer qualifizierten Aufbereitung als Recyclingmaterial wiederverwendet werden zu können. Die SER GmbH führt im Unternehmensverbund Erdund Rückbaumaßnahmen durch, wodurch sich der Kreis zwischen Rückbaumaßnahmen und mineralischer Aufbereitung schließt. Der Unternehmensverbund mit über 250 Mitarbeiterinnen und Mitarbeitern verfügt über vier eigene Aufbereitungsanlagen und bewältigt an drei Produktionsstandorten einen Massenstrom von jährlich rund 1,5 Mio. t.
Für seine Bemühungen in der Aufbereitung von Altschotter wurde die RUZ 2021 von der Deutschen Bahn zum Lieferanten des Jahres im Bereich Umwelt ausgezeichnet.
- Prozessindustrie
- Verarbeitungsprozess ,
- Entsorgung / Recycling
- GreenTech BW ,
- Prozessoptimierung ,
- Stoffkreislauf / Recycling
- Energie ,
- Material ,
- Abwasser ,
- Abfälle