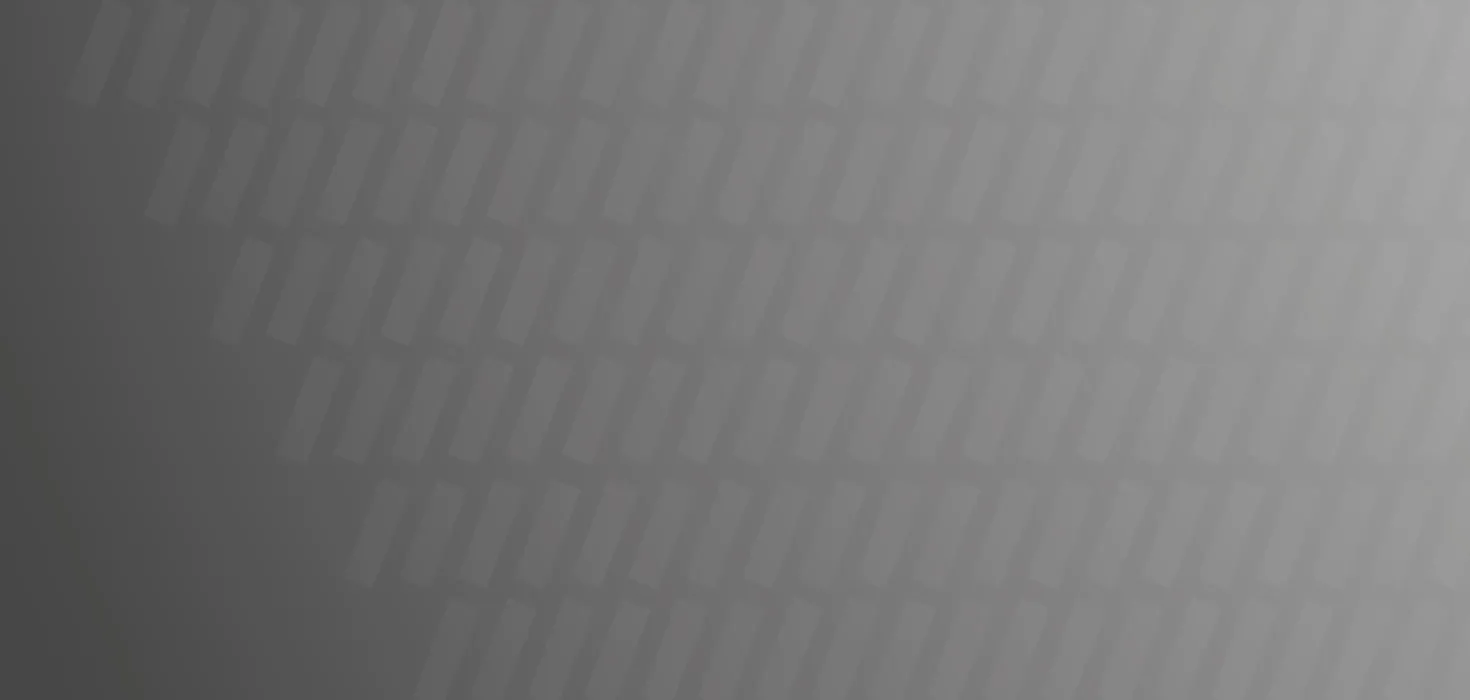
Ressourcenminimierung durch Teilautomation
Ausschussreduzierung von Lithiumzellen und Nickel-Verbindern
Die ANSMANN AG hat sich auf die Entwicklung und Fertigung individueller und mobiler Stromversorgungen spezialisiert. Der Prozessschritt der manuellen Punktverschweißung sollte in diesem Projekt optimiert werden, um die Ausschussrate zu verringern. Durch den Einsatz einer automatischen Widerstandspunktschweißanlage konnte das Unternehmen dieses Ziel umsetzen.
Kostenvorteile
über 50.000 Euro/Jahr
Als Systemlieferant hat sich die ANSMANN AG auf die Entwicklung und Fertigung individueller und mobiler Stromversorgungen spezialisiert. Mehr als 20 Jahre Erfahrung machen ANSMANN zum Experten rund um Akkus, Akkupacks, Primärbatterien, Ladegeräte und Netzteile. ANSMANN entwickelt auf Kundenwunsch alle Komponenten, die Hard- und Software sowie die Mechanik und übernimmt die Zertifizierung der Systeme. Unter anderem ist ANSMANN für Gerätehersteller in den Bereichen Antriebssysteme, Medizintechnik und Gartengeräte tätig.
Bei der Akkuproduktion ist die Rationalisierung der Fertigung durch den globalen Preisdruck das dominierende Thema. Angesichts dessen sollten notwendige Investitionsentscheidungen auch die Ressourceneffizienz des Verfahrens berücksichtigen. Des Weiteren sollte vor diesem Hintergrund das Produktdesign ebenfalls überprüft werden. Als wesentlicher Ansatzpunkt zur Steigerung der Ressourceneffizienz hat sich hierbei das Verschweißen der Akkupacks erwiesen.
Im manuellen Punktschweißverfahren ist ein hoher Ausschuss oftmals unvermeidbar. Besonders im Bereich der Lithiumzellen spielt das eine große Rolle, denn defekte Lithiumzellen sind Sondermüll. Daher sind Lithiumzellen nicht nur sehr teuer und aufwendig herzustellen und zu beschaffen, sondern auch zu entsorgen. Die Zielsetzung war somit vor allem die Steigerung des Wirkungsgrads und die Minderung des Produktionsausschusses. Die angestrebte Lösung lag daher nicht nur in steigenden Stückzahlen begründet, sondern war auch aufgrund der Prozessabsicherung erforderlich.
Der Prozessschritt der manuellen Punktverschweißung wurde auf den Prüfstand gestellt. Durch den Einsatz neuer und energieeffizienter Widerstandspunktschweißmaschinen sollte zum einen der Wirkungsgrad der Maschinen verbessert, zum anderen der Komponentenausschuss deutlich reduziert werden.
Die Umsetzung der Idee erfolgte durch den Einsatz einer automatischen Widerstandspunktschweißanlage. Durch den neu eingeführten, stabilen und reproduzierbaren Schweißprozess lassen sich die benötigten Materialen besser und effektiver nutzen. Im Zuge der Automation wurden die angrenzenden Prozesse ebenfalls optimiert. Die eingesetzten Anlagen sind speziell für kleine und mittelgroße Produktionslose geeignet. Sie unterscheiden sich dabei von den Großserienanlagen asiatischer Wettbewerber. Neben dem reproduzierbaren Automationsprozess sind die Anlagen mit den neuesten Widerstandspunktschweißköpfen ausgestattet, welche Schwankungen im Aufbau des Akkus ausgleichen und somit die Ressourceneffizienz erhöhen. Dadurch entfällt das Finden der Schweißparameter anhand von Mustern. Die eingesetzte Lösung wurde aus anderen Anwendungsbereichen übertragen und mit eigener Sensorik auf die diffizilen Schweißparameter aufgerüstet.
Mit dem Aufbau und der Dimensionierung der Anlagen lassen sich sowohl sehr große Akkupacks, als auch eine Vielzahl von kleinen Akkupacks gleichzeitig auf einer Anlage bearbeiten. Die eingesetzten Maschinen sind auch auf die Weiterentwicklung der Batteriebranche hin ausgerichtet, was vor allem zukünftige Baugrößen und Zellchemien betrifft. Die vorhandenen Maschinen wurden auch angeschafft, um Spezialanwendungen, wie z. B. LiFe-Akkus (Lithium-Eisen), verarbeiten zu können. Damit werden auch zukünftig Ressourceneinsparungen bei Lithiumzellen ermöglicht. Die gesamte Maßnahme wurde von Mitarbeitern der ANSMANN AG geplant und umgesetzt. Die Anlagen gingen in den Jahren 2015 und 2016 in Betrieb.
Der Erfolg der umgesetzten Maßnahmen wird durch die Höhe der Materialeinsparung deutlich. Die grundlegende Überarbeitung und Automatisierung des Widerstandspunktschweißprozesses führen zu Einsparungen in allen Bereichen. Bezogen auf den bisherigen Ausschuss wurde der interne Ausschuss von Lithiumzellen und Nickel-Verbindern durch die eingesetzte Automatisierung um mehr als 90 % drastisch verringert, womit monetäre Einsparungen in Höhe von über 50.000 Euro pro Jahr erzielt werden. Außerdem lassen sich die Nickel-Verbinder durch die generelle Konstruktionsverbesserung und Standardisierung zukünftig einfacher und besser fertigen. Dies schont die Ressourcen in der Wertschöpfungskette. Hierbei muss außerdem angemerkt werden, dass durch die ressourceneffizientere Produktion wirtschaftskritische Rohstoffe, wie Lithium, Kobalt und Nickel, eingespart werden.
Bei der aufwendigen Gewinnung von Lithium und der Herstellung von Li-Ionen Zellen entstehen Treibhausgase und Schadstoffemissionen. Durch Abfallvermeidung und Materialeinsparungen werden diese mit der Rohstoffbereitstellung verbundenen Umweltwirkungen reduziert. Insgesamt werden nun jedes Jahr mehrere 10.000 Lithiumzellen, über ein Kilometer Verbindermaterial und mehrere Tausend Kilometer Klebebänder und Isoliermaterial eingespart. Damit einhergehend konnte der Energieverbrauch deutlich gesenkt werden.
Oftmals ist der Ausgangspunkt für Optimierungen, das Bestreben im Sinne der Umwelt zu handeln. Diese Optimierungen sind darüber hinaus jedoch auch wirtschaftlich und energetisch sinnvoll und wichtig. Das zeigt insbesondere das Beispiel des Materialausschusses im Bereich der Lithiumzellen. Die Annahme, dass manuelle Verfahren für kleine und mittlere Losgrößen optimal sind, wurde widerlegt. Speziell die Herangehensweise, mit Weitblick und Umweltbewusstsein an Prozessoptimierungen zu arbeiten, stellte sich als richtiger Weg heraus. Schließlich konnte durch die kontinuierliche Verbesserung der Produktionsprozesse und die erhöhte Prozessbeherrschung die Wettbewerbsfähigkeit der Akkuherstellung gesichert werden, so dass diese Zukunftstechnologie auch weiterhin am Standort Baden-Württemberg erhalten bleibt.
Seit ihrer Gründung im Jahr 1991 kann die ANSMANN AG auf eine beeindruckende Firmenentwicklung zurückblicken. Von Edgar Ansmann als Ein-Mann-Betrieb im heimischen Wohnzimmer gegründet, hat sich das Unternehmen vom Start-up zum Weltmarktführer für Akku- und Ladetechnik entwickelt. An weltweit acht Standorten beschäftigen sich knapp 400 Mitarbeiterinnen und Mitarbeiter in den Geschäftsbereichen Consumer Electronics, Industrial Solutions und E-Mobility mit maßgeschneiderten Systemlösungen. An Standorten in Deutschland und Fernost werden Produkte entwickelt und produziert, die genau auf die Bedürfnisse der Kunden abgestimmt sind.
Der Einsatz von neuesten Technologien in der Forschung & Entwicklung sowie eine reibungslose Logistik gewährleisten, dass das richtige Produkt in der richtigen Qualität zum richtigen Preis zur richtigen Zeit am richtigen Ort ist. Durch strategische Produktplanung und passende Werbeaktivitäten sorgt das Marketing für eine markt- und kundenorientierte Ausrichtung der Unternehmensaktivitäten und leistet damit einen wichtigen Beitrag zum Erfolg der ANSMANN AG. Entwickelt von hochqualifiziertem Personal am Stammsitz im baden-württembergischen Assamstadt erfüllen ANSMANN Produkte höchste Qualitätsansprüche, auf die auch zahlreiche namhafte Kunden aus Industrie und Handel seit vielen Jahren vertrauen.

- Großserienfertigung
- Verarbeitungsprozess
- Produktinnovation ,
- Ausbeuteerhöhung
- Energie ,
- Material ,
- Metalle ,
- Abgas
- taktisch (1 bis 5 Jahre)