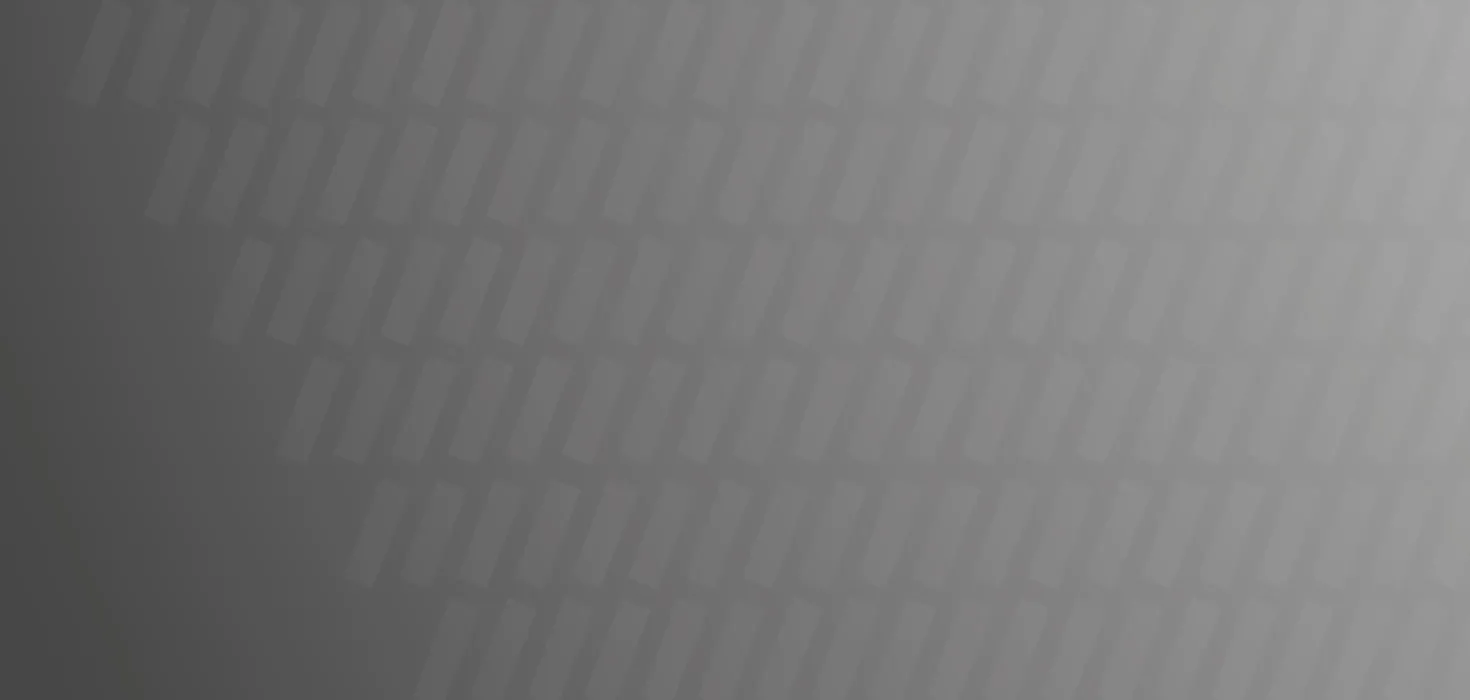
Systematische Energieeffizienzverbesserung von Lüftungsanlagen
Energiebedarfsreduktion
Die EvoBus GmbH produziert Stadt- und Reisebusse. An ihrem Standort in Mannheim hatte das Unternehmen bis jetzt einen hohen Energiebedarf, was vor allem auf die Lüftungstechnik der Gebäude zurückzuführen ist. Darum hat sich das Unternehmen das Ziel gesetzt seine Lüftungstechnik so weit zu optimieren wie möglich, was zu hohen Energieeinsparungen geführt hat.
In sehr vielen Unternehmen ist die Lüftungstechnik für einen wesentlichen Anteil des Gesamtenergiebedarfs verantwortlich. Insbesondere bei Unternehmen mit geringer Energieintensivität kann der Anteil, z. B. bei hohem Gebäudebestand, auf weit über 50 % ansteigen. Die Lüftungstechnik ist somit einer der wesentlichen Stellhebel für die Verbesserung der Energieeffizienz im Betrieb.
Die EvoBus GmbH produziert am Standort Mannheim Stadt- und Reisebusse. Die Produktionsprozesse sind mit Ausnahme einzelner energierelevanter Fertigungsschritte nicht der treibende Faktor für den Energiebedarf des Standorts. Vielmehr wird auch hier ein Großteil der benötigten Energie für den Gebäudebetrieb – insbesondere der Lüftungstechnik – aufgewendet.
Daraus entstand die Zielsetzung, systematisch alle heute bekannten wirtschaftlich umsetzbaren Möglichkeiten zur energetischen Optimierung von Lüftungstechnik zu analysieren und in einen Best-Practice-Leitfaden zusammenzufassen. Dieser soll sowohl den Anlagenbetreibern, als auch dem Energiemanagement sowie den Lüftungsanlagenplanern als Hilfsmittel dienen, um dauerhaft die Energieeffizienz der Alt- und der kommenden Neuanlagen zu verbessern. Die Erreichung eines guten Return on Invest bei optimierten Lebenszykluskosten steht hierbei stets im Fokus.
Im Rahmen von Inhouse-Workshops mit anderen Betreibern aus dem Bereich Energie- und Facility Management wurden Grundparameter (Temperaturanforderungen, Luftwechselraten) für den Betrieb von Lüftungsanlagen in den klassischen Produktionsbereichen im Automobilbau zusammengetragen und diskutiert. Darüber hinaus entstand ein Best-Practice-Leitfaden, der die systematische Vorgehensweise zur Verbesserung der Energieeffizienz der Lüftungsanlagen beschreibt. Dieser Leitfaden beinhaltet ein Konzept mit drei Schritten.
In Schritt eins werden vorwiegend organisatorische Maßnahmen hinsichtlich ihrer Anwendbarkeit überprüft. Hierunter fallen die Anpassungen von Anlagenlaufzeiten und die Reduzierung von Luftmengenraten an den tatsächlichen Bedarf. Der Eingriff in die Anlagenprogrammierung, zum Beispiel zur Optimierung von Mischluftregelungen, wird ebenfalls in diesem Schritt untersucht.
In Schritt zwei wird geprüft, ob eine wirtschaftliche Substitution der Lüftungstechnik vorgenommen werden kann, ohne dass die Arbeitsplatzanforderungen vernachlässigt werden. Hierzu zählen die Optimierung der Luftzuführung zu den Arbeitsplätzen, die Nutzung freier Lüftung mittels steuerbarer Dachöffnungen (wie Notrauchanlagen), Tore und Fenster sowie die Nutzung von Strahlungsheizungen (z. B. Deckenstrahlplatten oder Dunkelstrahler).
Erst nachdem die vorab beschriebenen Potenziale überprüft wurden, macht eine Investition in verbesserte Anlagentechnik Sinn. Daher werden erst in Schritt drei die Reduzierung des Strombedarfs von Lüftungsmotoren mittels Frequenzumrichter, Keilriemen- bzw. Flachriemenantrieb und Hocheffizienzmotoren, die Installation von Wärmerückgewinnungssystemen, der Einsatz effizienter Filtertechnik und weitere technische Maßnahmen auf ihre Wirtschaftlichkeit hin überprüft.
Im ersten Schritt wurde eine Aufnahme der bestehenden Anlagentechnik vorgenommen und deren aktuelle Steuerungs- und Regelungsfunktionen überprüft. Im Zuge dessen wurden außerdem die jeweils versorgten Bereiche hinsichtlich der Arbeitsaufgaben und -prozesse kategorisiert, um einen Abgleich zwischen Ist-Zustand und Soll-Zustand zu ermöglichen. Aufgrund dieser Informationen, und des zuvor erarbeiteten Best-Practice-Leitfadens, konnte jede Anlage systematisch auf das derzeit wirtschaftliche Optimum gebracht werden. Jede Maßnahme wurde durch ausgiebige Messungen der klimatischen Bedingungen (Temperatur, Feuchte, CO2) vor und nach der Umsetzung begleitet. Umsetzungsbeteiligt waren vorwiegend Mitarbeiter aus den Bereichen Facility Management, Gebäudeleittechnik und Energiemanagement. Jedoch wurde auch sorgsam darauf geachtet, dass jede Änderung zuvor mit den jeweiligen Nutzern und den zuständigen Arbeitnehmervertretern besprochen wurde.
Im Jahr 2012 begann im Rahmen des Energiemanagements am Standort die systematische Anwendung des Best-Practice-Leitfadens. Neben weiteren Projekten in anderen Gewerken war dies der wichtigste Baustein, um die Energiebedarfsreduzierung um ca. 28 % zu erreichen. Im Vergleich Ende 2015 mit dem Basisjahr 2011 konnten nunmehr bereits 25 GWh Energie eingespart werden.
Einer der ersten Bereiche, in dem der Best-Practice-Leitfaden angewandt wurde, war der Bereich Auslieferungshalle. In dieser ca. 2.700 m² großen Halle werden die in Mannheim gefertigten Busse an den Kunden übergeben. Somit sind die Anforderungen an die Luftqualität verlässlich einzuhalten. Hier konnte eine deutliche Reduzierung des Wärmebedarfs der Halle, unabhängig von den Wettereinflüssen erreicht werden.
Die wichtigste Erkenntnis im Rahmen dieses Projektes war, dass ein zielgerichteter, effizienter Anlagenbetrieb nur möglich ist, wenn Anlagentechnik und -prozesse verstanden werden. Darüber hinaus müssen auch kontinuierliche Anpassungen an den Bedarf vorgenommen werden. Das stetige Hinterfragen der aktuellen Anlageneinstellungen und der vermeintlichen Nutzeranforderungen bringt oftmals bisher schlummernde Potenziale zum Vorschein. Unbewusste Fehler, zum Beispiel durch unzureichend kommunizierte Änderungen bei der Hallenbelegung, fallen meist nur dann auf, wenn der Bedarf nicht mehr erfüllt wird. Die unmittelbare Erkennung von Überversorgung ist schwieriger, doch einer der wichtigsten Stellhebel für einen effizienten Lüftungsanlagenbetrieb. Ein nicht zu vernachlässigender Faktor ist allerdings auch die Nutzerzufriedenheit. Aufgrund ausgiebiger Kommunikation der Maßnahmen im Vorfeld und im Nachgang der Umsetzung konnte hier ein gemeinsames nachhaltiges Bewusstsein und Verständnis geschaffen werden.
Die EvoBus GmbH ist als das größte europäische Tochterunternehmen der Daimler AG verantwortlich für die europäischen Busaktivitäten des Daimler-Konzerns. Mit dem Zusammenschluss der Marken Setra und Mercedes-Benz wurden im Jahr 1995 die Weichen für den Erfolg der EvoBus GmbH gestellt. Mercedes-Benz, der Erfinder des Omnibusses, und Setra, die ehemals unter dem Namen Kässbohrer bekannte Traditionsmarke, gehören zu den Pionieren des Omnibusbaus.
Mit zahlreichen Produktionsstandorten und Servicestützpunkten ist EvoBus mit mehr als 8.000 Mitarbeiterinnen und Mitarbeitern in Europa vertreten. Als Teil des Geschäftsfelds Daimler Buses ist die EvoBus GmbH in die weltweiten Busaktivitäten des Daimler-Konzerns eingebettet.
Als Full-Line-Anbieter deckt das Unternehmen alle Bedürfnisse im Bussegment ab und bietet für jede Kundenanforderung die beste Lösung. Zum Produktportfolio gehören Stadt-, Überland- und Reisebusse sowie Fahrgestelle. Passend dazu wird mit der Dienstleistungsmarke OMNIplus ein busspezifisches Servicenetz und mit der Marke BusStore ein breites Angebot an Gebrauchtbussen angeboten.
Als Technologie- und Innovationsführer setzt die EvoBus GmbH Maßstäbe in Sachen Sicherheit, Komfort, Design und Umweltschutz. Seinen Kunden bietet das Unternehmen umweltverträgliche, effiziente und sichere Busse. Gleichzeitig hat EvoBus das Ziel, nachhaltige Antworten auf die Herausforderungen der Mobilität der Zukunft zu finden.

- Großserienfertigung
- Unterstützungsprozesse / Gebäudemanagement
- Energiekonzept
- Energie ,
- Abgas
- operativ (kleiner 1 Jahr)