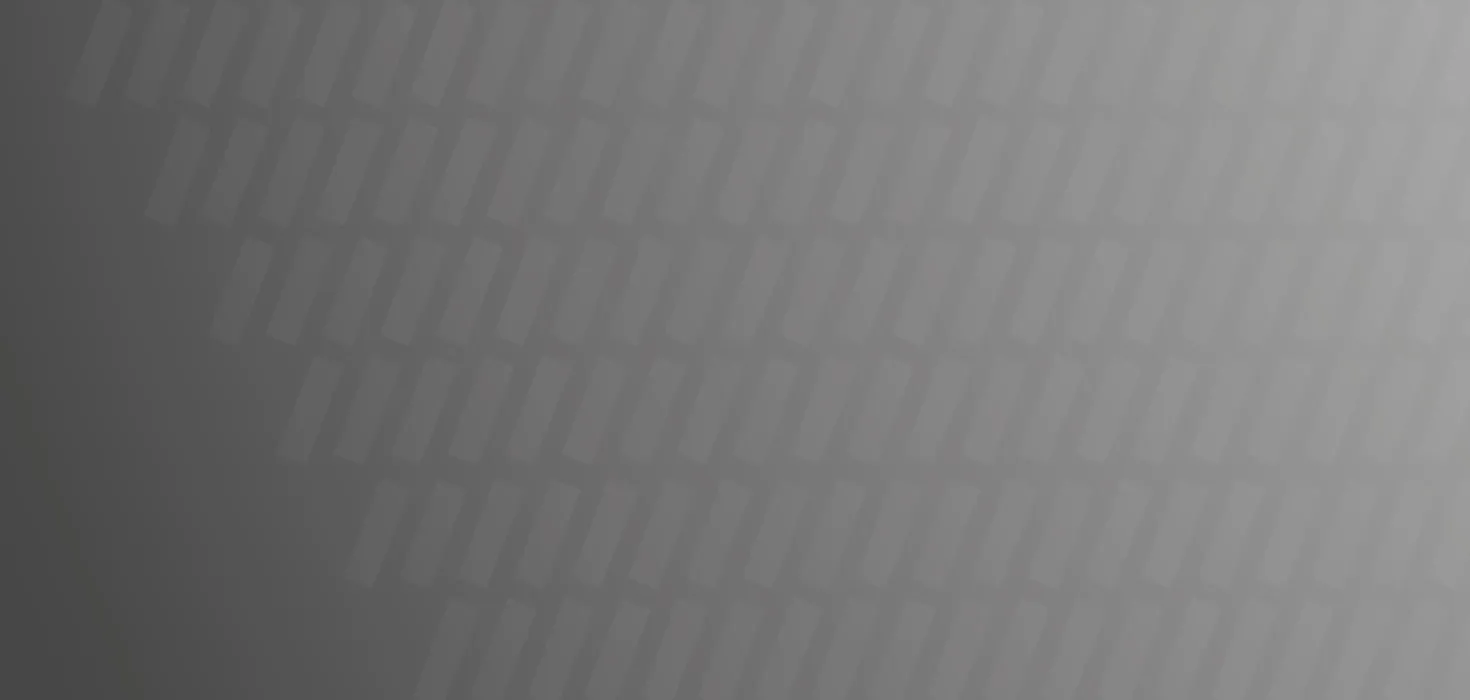
EEP und EEP2 – Siemens spart Energie durch Effizienzprogramme
Energieeinsparung (elektisch)
Energieeinsparung (Wärme)
Energieeinsparung (insgesamt)
CO2-Reduktion
Die Siemens AG hat sich das Ziel gesetzt, bis zum Jahr 2030 klimaneutral zu wirtschaften. Dafür wurde das Energieeffizienzprogramm (EEP) 1 und 2 geschaffen, um produktionsspezifische Einsparpotenziale aufzudecken und die Energieeffizienz des Unternehmens generell zu steigern. Im Zuge dessen wurden der Industriepark in Karlsruhe und das Siemens-Werk in Rastatt energetisch optimiert.
Der effiziente Umgang mit Ressourcen und das Eingrenzen von Umweltbelastungen, z.B. der CO2-Emissionen, zählen zu den großen Herausforderungen unserer Zeit. Umweltschutz, Energieeffizienz und damit ein optimierter Einsatz der Ressourcen sind wichtige Themen, auch für einen wirtschaftlichen und nachhaltigen Produktionsbetrieb. Die Siemens AG hat sich das Ziel gesetzt, bis zum Jahr 2030 klimaneutral zu wirtschaften. Um dieses Ziel zu erreichen, wurde von Siemens das Energieeffizienzprogramm (EEP) ins Leben gerufen. Das EEP deckt gebäude- und produktionsspezifische Einsparpotenziale auf und setzt zielgerichtet individuelle Maßnahmen um. Im Rahmen des EEP2-Programms, der Fortführung des EEP, werden von 2015 bis 2020 konzernweit 100 Mio. Euro für die Umsetzung von Effizienzmaßnahmen bereitgestellt, mit dem Ziel, den CO2-Ausstoß um 80.000 t pro Jahr zu reduzieren.
In Baden-Württemberg wurden bisher die Standorte Rastatt und Karlsruhe, einer der größten Standorte des Siemens-Konzerns weltweit, in das Programm aufgenommen. Hierzu hat die Abteilung „Energieeffizienzservice“ in Stuttgart die Einsparpotenziale in den einzelnen Werken ermittelt und Maßnahmenpakete für die jeweiligen Standorte ausgearbeitet. Dabei wurden alle Verbrauchsmedien wie beispielsweise Gas, Strom, Wasser, Druckluft und Kälte betrachtet. Mit dem EEP2 sollen letztlich Verbesserungen in den Bereichen Arbeitsbedingungen, Verfügbarkeit der Anlagen, Energieeffizienz und Umweltschutz erreicht werden.
Im Rahmen des EEP sollte an beiden Standorten eine hohe Anzahl von Einzelmaßnahmen auf dem Stand der Technik konsequent umgesetzt werden. Dazu sollte zunächst ein umfangreiches Mess- und Zählkonzept aufgebaut werden, um auf Grundlage der gesammelten Daten Optimierungen vorzunehmen und neue Einsparpotenziale erkennen zu können. Dies dient auch der fachgerechten Einregulierung und fortlaufenden Optimierung der Anlagen.
Neben der Minderung der Energiekosten sollte auch der Aufbau einer dezentralen Stromerzeugung ein wichtiger Aspekt der Maßnahmen sein. Entsprechend wurde der Einsatz von effizienten und zukunftsfähigen Techniken wie Kraft-Wärme-Kopplung und Kraft-Wärme-Kälte-Kopplung geplant. Schließlich sollten die Maßnahmen die wichtigsten Bereiche der technischen Gebäudeausrüstung umfassen. Von der Beleuchtung über Heizung, Kühlung und Lüftung bis zum Druckluftsystem sollten effiziente und bedarfsgerechte Lösungen umgesetzt werden.
Im Werk der Building Technologies in Rastatt wurden in zwei Maßnahmenpaketen insgesamt fast 2 Mio. Euro und im Industriepark Karlsruhe über 6,5 Mio. Euro zur Steigerung der Energieeffizienz investiert. Dies sind nicht zuletzt wichtige Schritte für die Zukunft der Standorte.
In beiden Werken wurde zunächst im Bereich der Mess-, Steuerungs- und Regelungstechnik eine große Anzahl an Fühlern und Zählern eingebaut, um über die Energie- und Betriebsleistungsplattform Siemens Navigator und die Gebäudemanagementplattform Siemens Desigo CC die Einsparpotenziale bzw. Einsparungen ermitteln und überprüfen zu können.
Zentrale Vorhaben an beiden Standorten betrafen jeweils die Optimierung der Wärmeversorgung. Dazu wurde in Rastatt ein älterer Heizkessel durch einen neuen hocheffizienten Gas-Brennwertkessel ersetzt. Außerdem wurde die Abwärme eines Heizkessels zum Test der dort gefertigten Feuerungsautomaten in das Heizsystem eingebunden und das Regelungskonzept der Heizkessel wurde überarbeitet und optimiert. Um eine Überhitzung der Werkhallen durch die Wärme im Sommer zu vermeiden, wurden die Kälteaggregate der Wellenlötmaschine mit Abluftleitungen ausgerüstet. Im Winter wird die Abwärme zur Beheizung der Halle verwendet.
Weiterhin wurde die Wärmeverteilung in den werkseigenen Wärmenetzen optimiert, um Verteilverluste zu reduzieren. Dazu wurden in Rastatt Heißwasserleitungen wärmegedämmt und die Heizungsunterverteilung in einem Bereich vollständig erneuert, während in Karlsruhe Pumpen sowie Ventile in der Heizzentrale ausgetauscht und die in Teilbereichen bestehende Lüftungsheizung durch Deckenstrahlplatten ersetzt wurde.
Die umfangreichsten Maßnahmen an beiden Standorten waren jedoch die Installation von erdgasbetriebenen Blockheizkraftwerken (BHKW). Neben der Minderung der Energiekosten und der umweltfreundlichen Versorgung der Werke mit Wärme und Strom war der Aufbau einer dezentralen Stromerzeugung ein Grund für diese Maßnahmen. In Rastatt wurde darüber hinaus das BHKW durch die Anbindung einer Absorptionskältemaschine und einem Rückkühlwerk zu einer Kraft-Wärme-Kälte-Kopplungs-(KWKK)-Anlage erweitert.
Dabei dient das Rückkühlwerk gleichzeitig zur Bereitstellung Freier Kälte bei niedrigen Außentemperaturen, was den Stromverbrauch weiter reduziert. Die im Kühlsystem des Karlsruher Standorts installierten Rückkühlwerke wurden über Wärmetauscher vom wassergefüllten Primärnetz separiert und werden nun mit einer Glykolmischung betrieben. Nicht mehr benötigte Kältemaschinen konnten dort somit demontiert werden.
Die Wärmeerzeugung wurde an beiden Standorten durch den Einbau einer Wärmerückgewinnung in die Druckluftkompressoren ergänzt. Des Weiteren wurden in Karlsruhe und Rastatt Druckluftleckagen behoben und die Produktionshallen wurden mit stromsparender LED-Technik und präsenzabhängiger Tageslichtsteuerung ausgestattet. Im Bereich der Raumlufttechnik (RLT) wurden die Antriebsmotoren der Ventilatoren ausgetauscht und durch hocheffiziente bedarfsgeregelte ersetzt. Außerdem wird nun in Karlsruhe der Volumenstrom bedarfsgerecht anhand der Konzentration von CO2 in der Luft geregelt.
Alle Maßnahmen sind über ein Gebäudemanagementsystem von Siemens vernetzt und erlauben so einen aufeinander abgestimmten und regelungstechnisch optimierten Betrieb der Anlagen.
Insgesamt spart die Siemens AG durch die beiden Effizienzprogramme EEP und EEP2 in Baden-Württemberg jährlich 2.461 MWh an elektrischer Energie und 5.530 MWh an Wärmeenergie. Durch die umgesetzten Maßnahmen konnte der Energieverbrauch insgesamt um ca. 55 % gesenkt werden. Entsprechend können durch die Einsparmaßnahmen ca. 1.800 t an CO2-Emissionen jährlich vermieden werden. Das steigert nicht nur die Wettbewerbsfähigkeit der Siemens AG, sondern leistet auch einen wichtigen Beitrag zum Umwelt- und Klimaschutz.

Die langjährige Projekterfahrung zeigt die Notwendigkeit einer detaillierten Kommunikation und frühzeitigen Abstimmung mit den Flächennutzern. Um in den Produktionsflächen Umbaumaßnahmen durchführen zu können, müssen im Vorfeld alle arbeitssicherheitsrelevanten Forderungen beachtet werden und es muss ein Vertrauensverhältnis zu den Produktionsverantwortlichen bestehen. Daher trägt die Analyse- und Planungsphase wesentlich zu einem reduzierten Aufwand in der Umsetzungsphase bei.
Weiterhin hat es sich als vorteilhaft erwiesen, dass alle Maßnahmen jederzeit zur Erhöhung der Gesamteffizienz um Komponenten ergänzt werden können. So wurden bereits weitere Effizienzmaßnahmen zur Ergänzung des Programms beauftragt. Außerdem kommen die Erfahrungen aus den laufenden Maßnahmen, insbesondere bei größeren Eigenerzeugungsanlagen sowie deren Genehmigung, zukünftigen Projekten zugute. Schließlich wird mit der Umsetzung eines Monitoringkonzepts projektbegleitend sichergestellt, dass sich die Maßnahmen in Rastatt und Karlsruhe in einer Gesamteinsparung aller beteiligten Siemens-Werke aufzeigen lassen, um jederzeit zur Umweltbilanz der Siemens AG aussagefähig zu sein.
Seit bald 170 Jahren findet die Siemens AG Wege, das Leben in vielen Bereichen zu verbessern. Der Siemens-Konzern ist heute in fast 200 Ländern vertreten und zählt weltweit zu den größten Unternehmen der Elektrotechnik und Elektronik. In Baden-Württemberg unterhält Siemens sieben Niederlassungen und fünf Fertigungs- und Entwicklungsstandorte.
Die Division Building Technologies von Siemens ist weltweit führend auf dem Markt für sichere, energieeffiziente und umweltfreundliche Gebäude und Infrastrukturen. Building Technologies verfügt über Angebote für Brandschutz und Sicherheit sowie Gebäudeautomation, HLK-Technik und Energiemanagement.
- Großserienfertigung
- Unterstützungsprozesse / Gebäudemanagement
- GreenTech BW ,
- Energiekonzept ,
- Dämmung / Isolation
- Energie ,
- Material ,
- Abfälle ,
- Abgas
- taktisch (1 bis 5 Jahre)